This article provides guidance on how to design steel columns subjected to combined axial compression and bending to EC3, using the simplified expressions in the IStructE manual for the design of steelwork buildings.
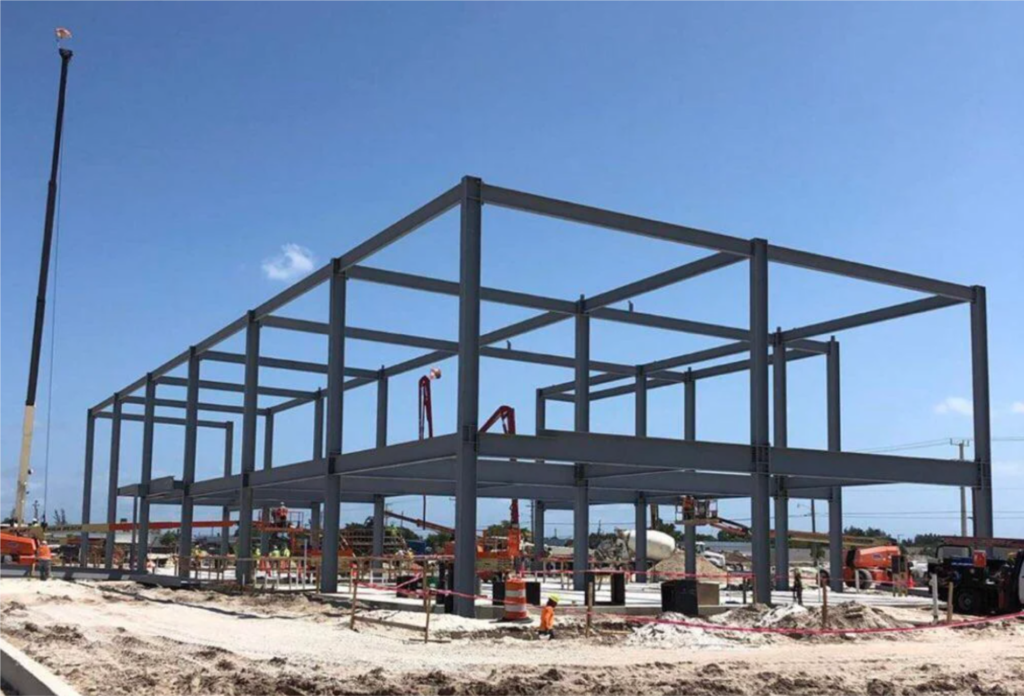
In steel frames, columns can be either in simple construction or not. When a column is in simple construction, steel connections are not allowed to transmit any significant bending moment. Lateral stability will be ensured by providing braced elements in the two orthogonal directions of the steel frame. This also implies that steel beams within the steel frame are designed as simply supported members, simplifying the design process. Thus, the columns are designed only for a combination of axial forces and nominal moments from the eccentricity of the transferred forces.
However, when a steel column is in an unbraced frame, where it must provide lateral stability in addition to the vertical forces it sustains, the joints are classified as moment connections. Therefore, the steel beams transmit significant moments to the steel columns. Hence, the steel beams can be designed to be continuous over the support.
A vast majority of steel columns in multi-Storey buildings are designed in simple construction. However, single Storey steel frames tend to be unbraced in one of the orthogonal directions (Such as in portal frames) necessitating the need for moment connections and the need to consider the steel column for additional moment.
How to design steel columns in simple connections has been presented in an earlier article See: Design of Steel Columns in Simple Construction. In this article, how to design a column subjected to combined axial load and bending would be explained.
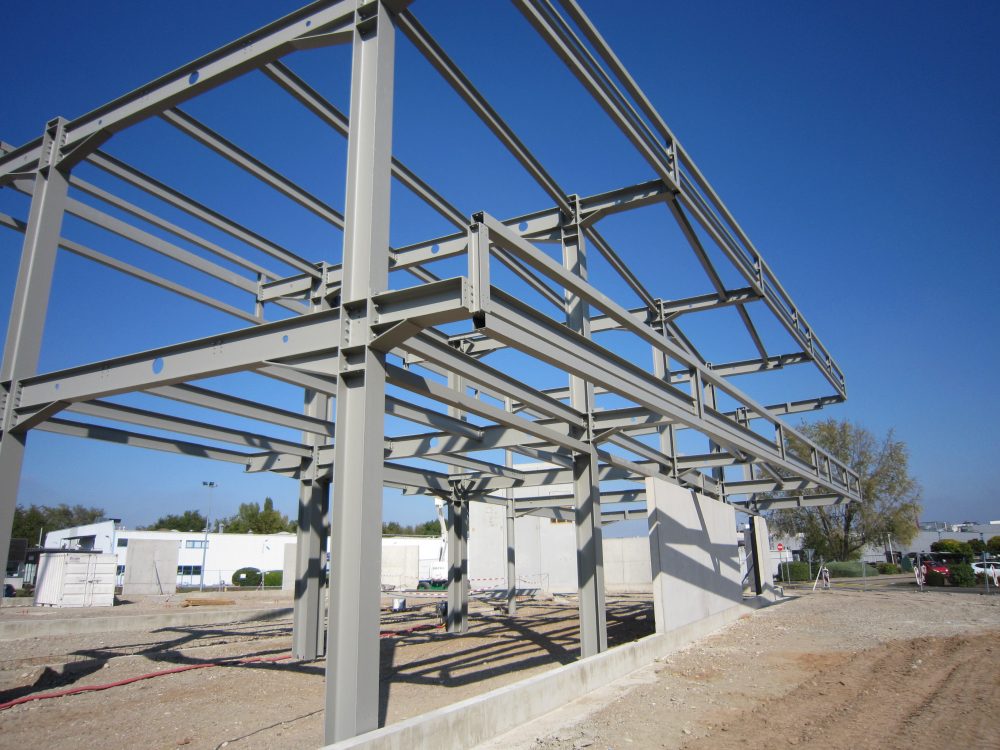
Verification of Column in Combined Axial Compression & Bending
There is an expression presented in clause 6.3.3(4) of BS EN 1993-1-1 for any steel sections subjected combined bending and compression applies for steel columns subjected to an axial load and bending moment. This expression requires so many complex variables that require the use of several charts to arrive at their appropriate values. However, there is a simplified but conservative expression provided in the Institution of Structural Engineer’s manual for the design of steel-work buildings, which can be used in place of clause 6.3.3(4).
The expressions are applicable for classes 1, 2, 3 & 4 cross-sections.
The expression is given as:
For open steel sections susceptible to lateral torsional buckling (I or H sections)
\frac { { N }_{ Ed } }{ { N }_{ min,b,Rd } } +\frac { { M }_{ y,Ed } }{ { M }_{ b,y,Rd } } +{C_{mz}}\frac { { M }_{ z,Rd } }{ { M }_{ z,Rd } } \le i
- For Class 1 & 2; i= 0.78
- For Class 2 & 3; i= 0.85.
For closed steel sections not susceptible to lateral torsional buckling (SHS & RSH sections)
\frac { { N }_{ Ed } }{ { N }_{ min,b,Rd } } +{C_{my}}\frac { { M }_{ y,Ed } }{ { M }_{ y,Rd } } +{C_mz}\frac { { M }_{ z,Rd } }{ { M }_{ z,Rd } } \le 0.85
Where:
- NEd is the applied axial load.
- My
,Ed is the applied bending moment in the y-y axis. - Mz
,Ed is the applied bending moment in the z-z axis. - Nmin,b
,Rd is the minimum axial buckling resistance. - Mb,y
,Rd is the flexural buckling resistance about the y-y axis. - Mz
,Rd is the bending moment resistance of the column in the z-z axis
Applied Actions
The applied axial load NEd can be determined using the tributary area method or by summing the vertical reactions from the steel beams framing into the column. Axial load reduction factors may also be applied in estimating the applied axial actions.
Bending moment applied in the y-y axis, My
Axial Buckling Resistance Nb,Rd
The axial buckling capacity of a steel column or a compression member is given as equation 6.47 of BS-EN-1993-1-1.
{ N }_{ min,Rd }={ \chi }_{ min }\frac { A{ f }_{ y } }{ { \gamma }_{ M1 } }
Where:
- fy is the yield strength of the steel section
- A is the cross-sectional area of the steel section
- χmin is the minimum reduction factor due to buckling. This is determined for both axes and the minimum selected.
- γM1 is the partial factor for the resistance of members subject to instability, which in the UK is set at 1.0
\chi=\frac { 1 }{ \left( \phi +\sqrt { { \phi }^{ 2 }-{ \lambda }^{ 2 } } \right) }
Where:
\phi =0.5\left[ 1+\alpha \left( \lambda -0.2 \right) +{ \lambda }^{ 2 } \right]
\lambda =\frac { { L }_{ cr } }{ i } \cdot \frac { 1 }{ { 93.9\varepsilon } }
- λ is the non-dimensional slenderness of the column
- Lcr is the unrestrained length of the column along the axis that is being considered.
- i is the radius of gyration about the axis that is being considered.
- ε is the coefficient for section classification
- α is the imperfection factor depending on appropriate buckling curve. This can be obtained from table 6.2 of BS EN 1993-1-
\varepsilon =\sqrt { \frac { 235 }{ { f }_{ y } } }
Flexural Buckling Resistance about the Major Axis
The flexural buckling resistance of a steel column is the same as that of a steel beam. This is described in Clause 6.3.2.1 (3) of BS EN 1993-1-1 in equation 6.55 as:
{ M }_{ b,y,Rd }={ \chi }_{ LT } M_{y,Rd}
M_{y,Rd}=\frac { { W }_{ y }{ f }_{ y } }{ { \gamma }_{ M1 } }
Where:
Wy is the major axis section modulus of the column section, which could be either elastic or plastic, depending on its classification. - χLT is the reduction factor that takes into account lateral torsional buckling.
{ \chi }_{ LT }=\frac { 1 }{ { \phi }_{ LT }+\sqrt { { \phi }_{ LT }-\beta { \lambda }_{ LT }^{ 2 } } }
{ \phi }_{ LT }=0.5\left[ 1+{ \alpha }_{ LT }\left( { \lambda }_{ LT }-{ \lambda }_{ Lt,0 } \right) +\beta { \lambda }_{ LT }^{ 2 } \right]
- The values of β and λLT,0 are defined as 0.75 and 0.4 respectively, as described in Clause NA.2.17 of the UK National Annex to BS-EN-1993-1-1
- αLT is the imperfection factor and is found in Table 6.3 of BS EN 1993-1-1, which relates to the steel column’s buckling curve.
- λLT is the non-dimensional slenderness of the column.
{ \lambda }_{ LT }=0.9\lambda
Flexural Resistance about the Minor Axis
The flexural resistance of a steel column about the minor axis is the same as that of a steel beam. This is defined as:
{ M }_{ z,Rd }=\frac { { W }_{ z }{ f }_{ y } }{ { \gamma }_{ M1 } }
Where:
- Wz is the major axis section modulus of the column section, which could be either elastic or plastic, depending on its classification.
Cmy and Cmz are uniform moment factors, they can conservatively be taken as 1.0. Less conservative values of these factors can be obtained by considering the values given in Annex B to EC3 Part 1-11.
Having determined the resistances to both axial forces and bending moments have been determined, the values can now be placed into the verification equation to determine the adequacy of the section to resist the load.
Also see: Designing a Laterally Unrestrained Steel Beam
Worked Example
An aesthetic perimeter steel column within a braced multi-Storey steel building is required to carry loads from a mezzanine cantilevered floor. The ultimate axial compressive load at this level is 1250kN and the applied design bending moment in both directions is 40kN.m and 8kN.m in the y-y and z-z directions respectively. Assuming the height of the floor is 3.5m. Verify the adequacy of a 200 x 200 x 12.5 SHS made from grade 275 Steel in sustaining the applied loads.
By inspection, this column is class one, therefore the rules for class one is valid.
Design Actions
The design axial compressive force load NEd=3450kN
Design bending moment about the major y-y axis, My,Ed = 40kN.m
Design bending moment about the minor z-z axis Mz,Ed = 8kN.m
Let’s start by determining the section resistances.
Axial Buckling Resistance
By Inspection, buckling will have the same magnitude about both axes, since trial section is SHS. Therefore, the minimum axial buckling resistance will be equal to the buckling resistance about the y-y or z-z axis.
{ N }_{ min,b,Rd }\quad = ={ \chi }_{ z }\frac { A{ f }_{ y } }{ { \gamma }_{ M1 } }
{ f }_{ y }={ R }_{ EH }=275/{ mm }^{ 2 }
\varepsilon =\sqrt { \frac { 235 }{ { f }_{ y } } } =\sqrt { \frac { 235 }{ 275} } =0.92
{ \lambda }_{ z }=\left( \frac { { l }_{ cr } }{ { i } } \right) \cdot \left( \frac { 1 }{ 93.9\varepsilon } \right)
=\frac { 3500 }{ 76.1 } \cdot \frac { 1 }{ 93.9\left( 0.92 \right) } =0.53
The buckling curve is determined from table 6.27 of BS EN 1993-1-1. Buckling curve, a applies, imperfection factor α=0.21
\phi =0.5\left[ 1+\alpha \left( \lambda -0.2 \right) +{ \lambda }^{ 2 } \right]
=0.5\left[ 1+0.21\left( 0.53-0.2 \right) +{ 0.53}^{ 2 } \right]\\ =0.68
\chi =\frac { 1 }{ \phi +\sqrt { { \phi }^{ 2 }-{ \lambda }^{ 2 } } }
=\frac { 1 }{ \left( 0.68+\sqrt { { 0.68 }^{ 2 }-{ 0.53 }^{ 2 } } \right) } =0.9
{ N }_{ min,b,Rd }={ \chi }_{ z }\frac { A{ f }_{ y } }{ { \gamma }_{ M1 } }
=0.9\times \frac { \left( 92.1\times 100 \right) \times 275 }{ 1.0 } =2279.5kN
Flexural Resistance about Major axis
{ M }_{ y,Rd }=\frac { { W }_{ pl }{ f }_{ y } }{ { \gamma }_{ M1 } }
\frac { \left( 643\times { 10 }^{ 3 } \right) \cdot 275 }{ 1.0 } =176.8kN.m
Flexural Resistance about minor axis
{ M }_{ z,Rd }=\frac { { W }_{ pl }{ f }_{ y } }{ { \gamma }_{ M1 } }
=\frac { \left( 643\times { 10 }^{ 3 } \right) \times 275 }{ 1.0 }=176.8kN.m
Member Verification
\frac { { N }_{ Ed } }{ { N }_{ min,b,Rd } } +{C_{my}}\frac { { M }_{ y,Ed } }{ { M }_{ y,Rd } } +{C_mz}\frac { { M }_{ z,Rd } }{ { M }_{ z,Rd } } \le 0.85
\frac { 1250 }{ 2279.5 } +1.0\frac { 40}{ 176.8 } +1.0 \frac { 8 }{ 176.8 }
=0.82<0.85\quad o.k
Since the expression is satisfied, thus a 200 x 200 x 12.5 SHS is adequate and may be adopted.
See: Design of Steel Elements in Axial Compression to EC3
Sources & Citation
Institution of Structural Engineers (2010). Manual for the Design of Steel-work Buildings to Eurocode 3.