This article provides an overview of the construction methodology and key considerations that built the deepest habitable grade commercial building in the world – The Londoner Hotel.
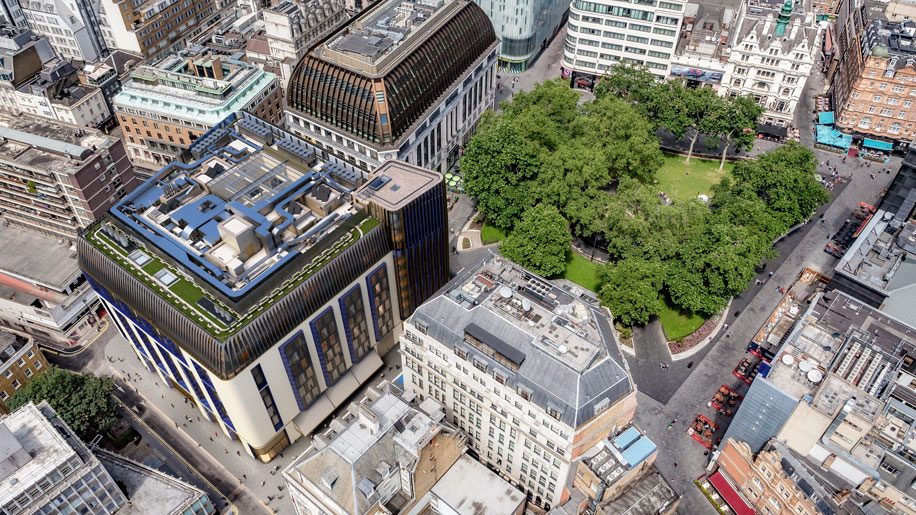
In the city centre of London, on Leicester square lies a new major development – The Londoner Hotel (see featured image). The luxurious five-star hotel which opened sometimes in 2021 holds 350 bedrooms, and suites, multiple restaurants and lounges, a roof top bar, spa with swimming pools and two integrated Odeon cinemas. The property is owned by the Edwardian Hotel, London.
Many of the aforenoted amenities are housed within the basement of the building which consist of six levels and stretches to over 30m below ground level (Figure 2). This building has nearly half of its floor area located below ground level, making it one of the deepest habitable grade basements in the world.
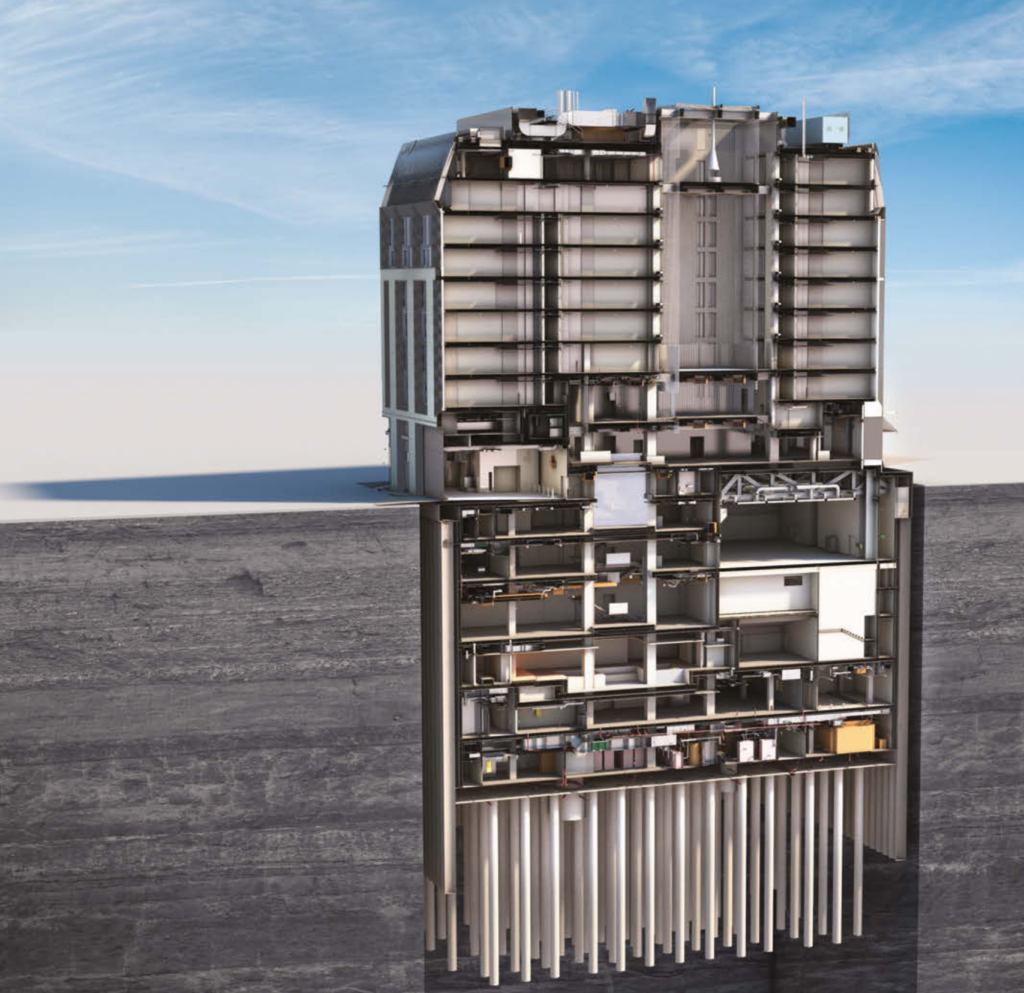
In this article, we shall focus on the construction methodology and considerations associated with building a deep basement, not just within the city centre of London, but on a very constraint site.
The Site
The site is a 50m x 50m plot consisting of 12 existing buildings, each of which had a shallow basement. At inception, these buildings were to be demolished to allow for the construction of the hotel. The plot had huge value and good prospects but not without constraints. First, the site is located in the densely populated, constricted city centre, posing a challenge for construction. Secondly, there was a tunnel 14m below ground level around the northwest location, restricting the size of basement that could be introduced in this location. Thirdly, and in fact more critical, the development was subject to a height restriction due to the site being located within a viewing corridor. Viewing corridors exists to protect views of monumental or heritage buildings from certain strategic locations around a city. Thus, the height of the proposed development had a preset limit of 36m or about nine floors above ground level.
Now, considering the client brief which sort to create bars, restaurants, leisure facilities and 350 bedrooms, in-short a high-class hotel, and cognizing the aforenoted site constraints, it became apparent that a deep basement might be the only solution to making the project viable.
The building was designed by Arup, McGee was the contractor in charge of constructing the basement and building frame.
Construction Methodology
Top-Down or Bottom-Up Construction
There are two main construction techniques in the construction of deep basements: Top-down and bottom-up. A basement’s design relies heavily on the method and order of construction, which must be considered up front.
In top-down construction, piles and plunge columns are installed from the ground up to the basement formation level before the ground floor slab is cast. After undermining the ground-floor slab and excavating to the next basement slab level, the first basement level is cast. The excavation and floor slab construction operation are repeated until the formation level is attained (See Video 1).
One of the main benefits of top-down construction is the opportunity for program savings because work on the superstructure can always be done concurrently with the development of the basement. The installation of permanent prop slabs as the excavation proceeds eliminates the requirement for a temporary propping system and aids in minimizing ground movement. These advantages, however, typically result in higher building costs. The vertical tolerance of plunge columns in this method can result in significant column areas on the lower floors of the basement, which can be a major disadvantage.
In contrast to top-bottom, bottom-up construction requires a phased sequence of excavation and the placement of temporary supports as the dig advances to the entire depth of the basement (See Video 2). Working from the bottom-up, this enables access to build the foundations before putting in permanent prop slabs. It also enables the dig to go more quickly than with the top-down approach, although superstructure construction cannot begin until the basement excavation is finished. To enable the basement to be built around the temporary props, their placement needs to be properly planned.
For the designers of the Londoner Hotel, deciding between top-down and bottom-up basement construction was not an easy pick. The design team first worked with contractors who preferred a top-down strategy. Later, however, analysis would determine that this approach was less preferable for two key reasons:
- It is anticipated that building of this size would have numerous transfer structures. This meant that loads are mostly supported by a small number of the basement columns. The designers considered placing 2.4m diameter piles beneath these heavily loaded columns as a top-down strategy. However, the transfer structures would still have need for additional temporary plunge columns to support them at intermediate locations until the raft slab was cast because these piles couldn’t handle the heavy loads.
- Only temporary loads could have been supported on the plunge columns prior to the raft slab being cast and covered in concrete. The finishing and fit-out that could have been completed on the superstructure floors prior to this milestone would have been constrained as a result.
These two considerations limited the advantages that could have easily been achieved using a top-down method, hence the decision to adopt a bottom-up construction approach.
Basement Excavation
Utilizing a bottom-up construction approach, entailed the removal of 75 000m3 of London clay, excavated prior to construction, with up to 150 lorries removing spoil every day.
An 18-ton lorry left the site every four minutes during the operation to remove the earth, which was extremely effective. Technology was a major factor in McGee’s ability to do this task so quickly1.
- A bespoke vehicle inspection app was developed to ensure the fleet of lorries was fully operational.1
- The Locatu manager 2 was used to optimize the routing of vehicles, in combination with cameras located around the site to flag any potential vehicles blocking the route, allowing issues to be resolved quickly and minimize congestion around the site. 1
- Weight loading indicators on the vehicles highlighted when the maximum 18t limit was reached. 1
- A bespoke mobile dashboard was developed to allow everyone in the site team to see information regarding progress. 1
Piling
Foundation construction could start with piling for the raft slab once the basement’s formation level was reached. However, this did not happen without its own difficulties.
Excavation for the piles was carried out using a piling rig. The basement walls were temporarily restrained by steel props (Figure 3), which limited the basement’s height and access to its corners. The pile cages were transported to the site in portions that could be linked across the bore to ensure that the piles in these locations could be erected.
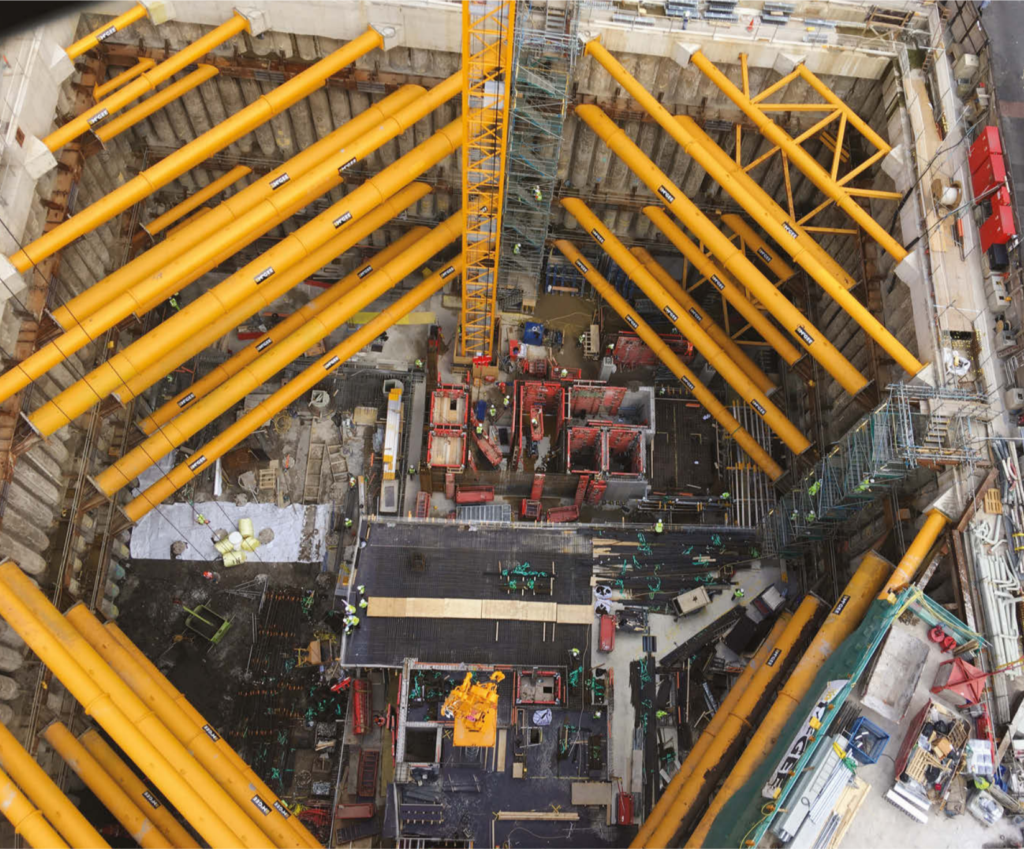
The pile placements were carefully planned so that cages could be threaded between the temporary props using a smaller piling equipment that could operate under them.
Fabrication and Installation of Transfer Structure
Up to the maximum of 356 406 1299 UC, sections were used to create the transfer trusses. Using bolted connections, it would have been challenging to join the trusses together on site. Additionally, welding the steel sections would have also been a very challenging and time-consuming on-site task. Therefore, full penetration butt welds (FPBWs) were created at the connections while the trusses were fabricated off-site (Figure 4).
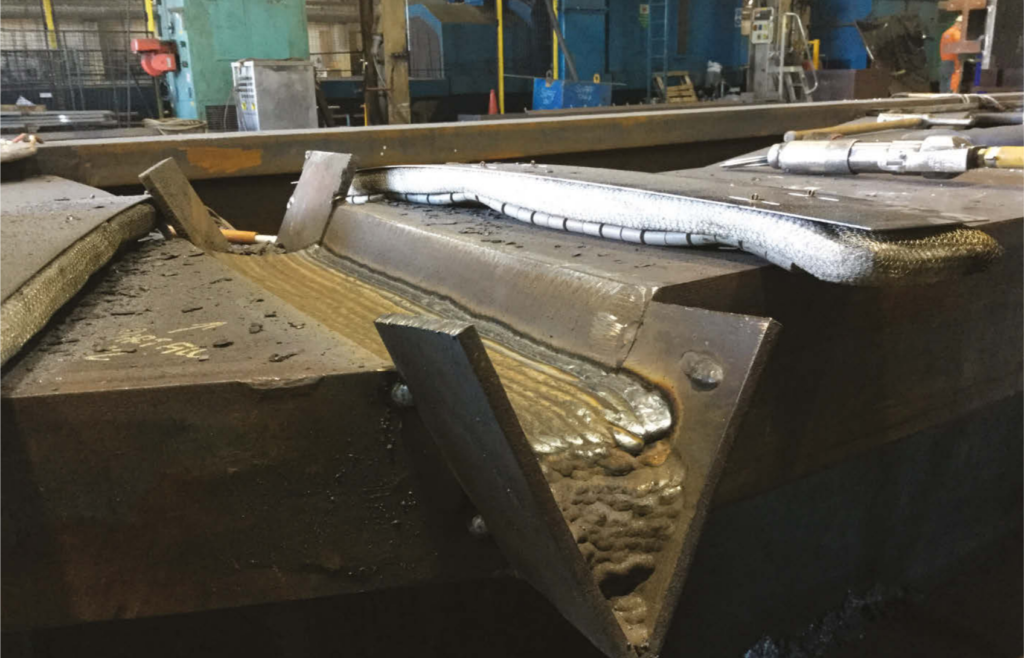
It is essential to carefully evaluate and manage welding steel of this type (HISTAR 460) and thickness (up to 140mm thick), and to establish specific welding techniques. Initial studies, in particular findings of low fracture toughness in the fusion line and heat-affected zone of the weld area, raised some questions about the weldability of HISTAR steel. In order to solve these issues, the fabricator, Allerton Steel, created pre-welding procedure requirements that balanced preheats, heat input, and inter-pass temperatures to achieve reduced hardness levels while retaining the welded material’s toughness. Thus, during fabrication, the amount of heat input was constrained, and this was continuously watched throughout the welding procedure. With a maximum Interpass temperature of 228°C and a high preheat of 125°C, welding occasionally has to be interrupted to avoid an excessive build-up of heat.
A full-scale test weld was performed to show that the welds would comply before the trusses were formed. Charpy impact tests were performed on samples obtained before and after the test weld to make sure the parent material’s toughness hadn’t diminished noticeably during the process. The largest FPBWs required up to 300 passes to complete. To ensure that all welds met the design specification, a strict non-destructive testing (NDT) procedure was implemented as follows:
- A visual inspection of every weld pass was undertaken by the welder, checking for cracks, pits, and various other aspects of the weld.1
- A hold time, defined as the time after weld completion before NDT testing may commence, of either 24 or 48 hours had to be observed depending on the carbon equivalence of the steel to allow any delayed cracking to occur.2
- Magnetic particle inspection was used to detect surface and shallow subsurface discontinuities. Undertaken on 100% of all large butt welds, this involves applying a magnetic field to the weld. A wet suspension of iron fi lings is applied to the weld and, if a discontinuity is present, magnetic flux leakage attracts the iron filings.3
- Ultrasonic testing was undertaken on 100% of all large butt welds. This involves projecting an ultrasonic sound wave through the weld at varying angles (0°, 45° and 60° normal to the steel face). The wave reflections are then measured on a calibrated oscilloscope, with any defects resulting in intermediate peaks on the display.4
Having completed fabrication, before erection, the welds underwent inspection by an unbiased examiner. The trusses were constructed off-site in complete 21m long pieces, making transportation through downtown London difficult and necessitating careful planning and the use of a mobile roadblock to move them to the site overnight. A 750t mobile crane was driven onto the ground-floor slab and used to raise the trusses into place. The slab was back propped to the foundation level at the base of the basement to prevent it from being overstressed by the high point loads of the crane outriggers.
Creating a Habitable Basement
According to BS 8102, basements are categorized from Grade 1 to 3 depending on their intended use and level of performance. The Londoner’s basement needed to attain a Grade 3 environment since it is inhabited by people and has high-value rooms, making it essential that there be no wetness. Contrary to a parking lot or plant room, where a certain amount of water penetration is permitted.
The basement has two ways of preventing groundwater intrusion (Figure 5). First, a substantial waterproof concrete liner wall which prevents majority of the water entering the basement. In addition, to this the liner wall with resists the enormous hydrostatic pressures that are transmitted to the prop slabs. Second, is a cavity that is insulated, vented, and drained. Any groundwater that enters into the cavity is permitted to flow to the basement’s floor, where it collects in a sump before being pumped out to the sewer.
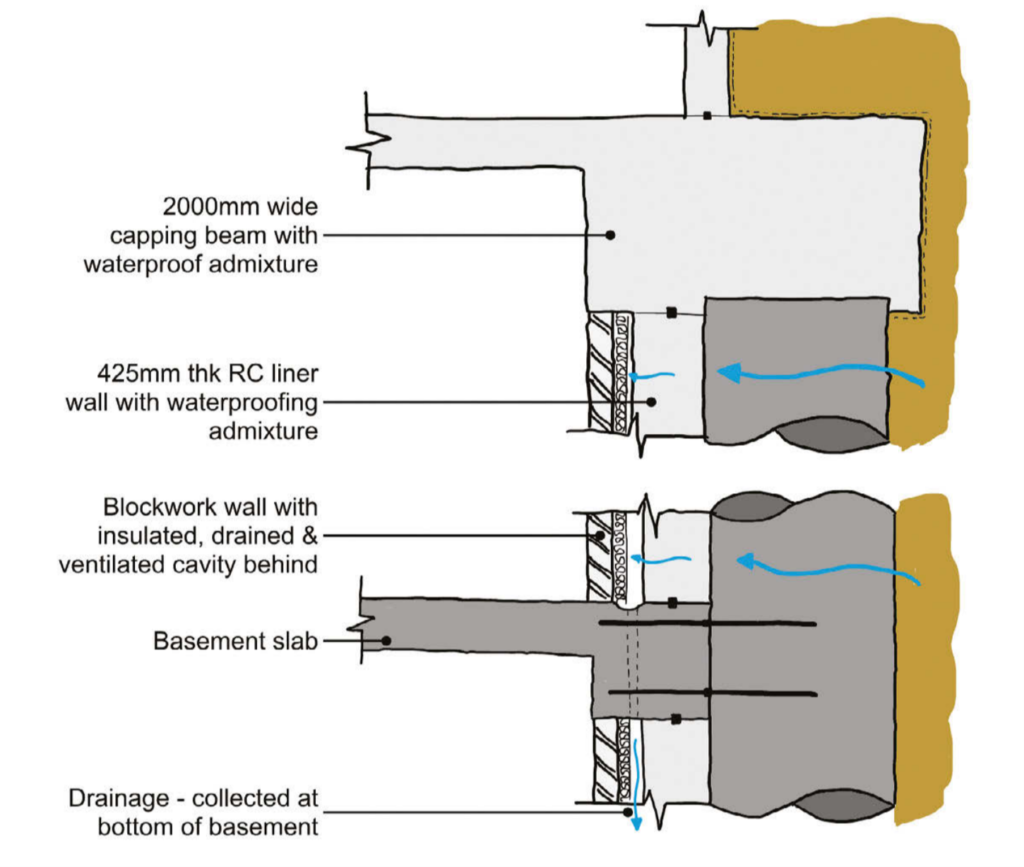
Conclusion
Perhaps, the biggest takeaway from the Londoner Hotel and for even buildings such as this is the fact that construction methodology is very important, which is why this article has deliberately dwelled almost entirely on this. The construction methodology is one of the most important factors when dealing with a complicated and constraints structure like the Londoner. Construction methodology must be incorporated from the very conceptual stages of the design. It will be crucial to comprehend the design’s drivers and possible contractors’ preferences.
On the Londoner Hotel, the designers, deciding between top-down and bottom-up construction had a significant impact on the anticipated ground motions, the size of the structural components, and the space needed for tolerances. On paper, Top-down would have appeared to be a suitable solution for this project, given the possible program benefits. However, it was clear from a closer look that this wasn’t the best course of action. The load inside the basement was concentrated in a few specific locations due to the numerous transfer structures, exceeding the capacity of the plunge columns. Should the designers have insisted on a Top-down method, the potential program savings typically associated with top-down construction would have been lost as a result of the necessity to install additional temporary columns and a restriction on the number of floors that could be created.
See: Reuse and Refurbish in the Climate Emergency: A Dossier of the Triton Square
Sources & References
Cooper R., Firth J., Nevil S., (2022) Digging Deep-Design and Construction of the Londoner Hotel. The Structural Engineer. The Institution of Structural Engineers [Online] Available at: www.istructe.org (Accessed: July 2022).