This article highlights some of the salient aspects of the design and construction of liquid-retaining structures in reinforced concrete
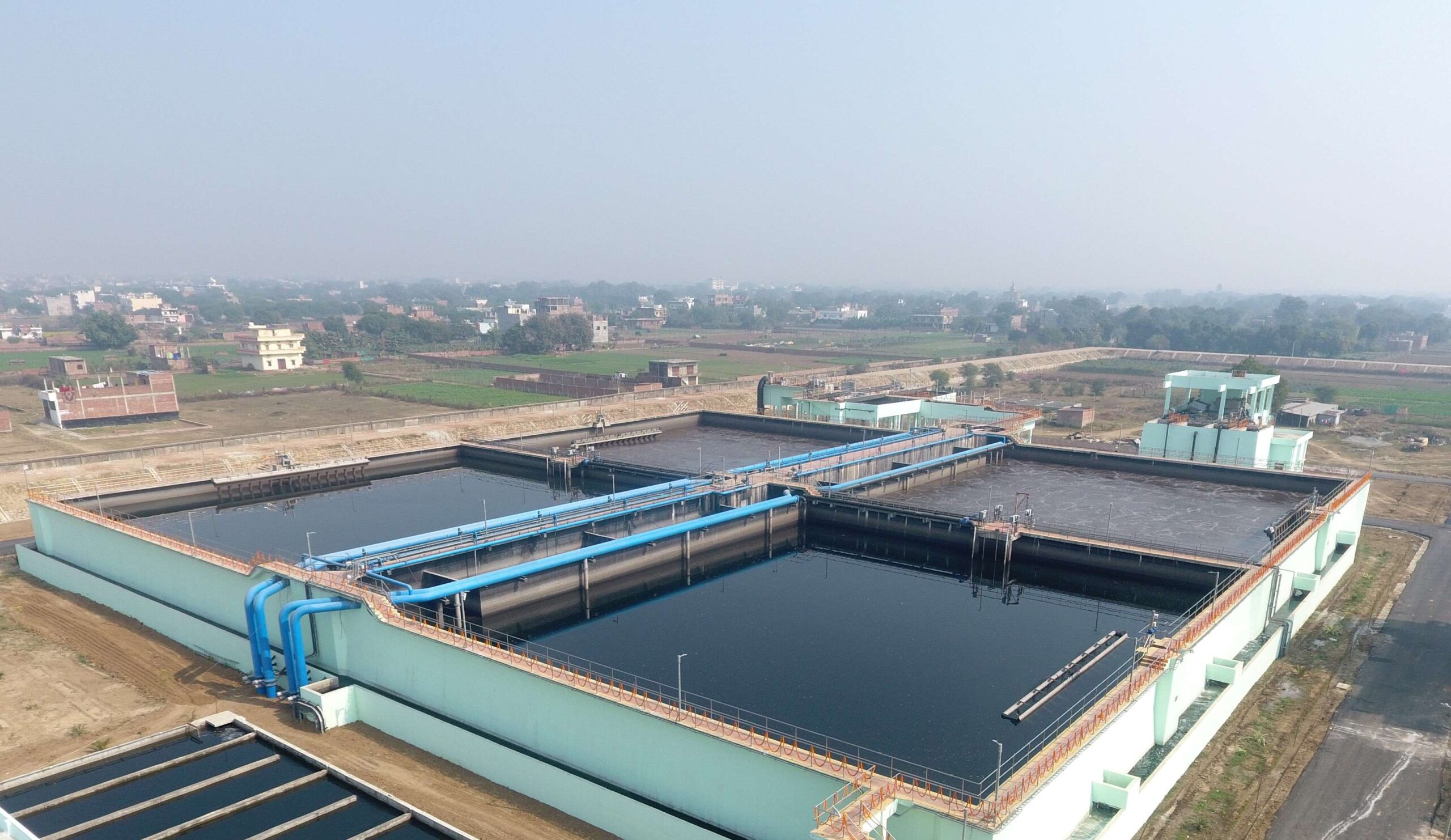
Liquid retaining structures are critical for the storage and management of various liquids, including water, chemicals, and industrial effluents. However, the structural design aspects of these structures differ slightly from those of other structures. Liquid retaining structures are containment structures, therefore, their design demands a thorough understanding of the serviceability limit states. For instance, most, liquid retaining structures must liquid-tight, hence, the crack widths have to be limited as much as possible.
This article highlights some of the salient aspects of the design and construction of liquid-retaining structures in reinforced concrete (See featured image). This article is based on Eurocodes BS EN 1992-1-11 and BS EN 1992-32 and the corresponding UK National Annexes. This is in no way an exhaustive treatment of the subject and the reader is advised to refer to The Concrete Centre book on concrete basements3 and CIRIA publication C6604 as basements and tanks which have many aspects in common with the subject.
Liquid-tightness
One of the most important considerations in the design of liquid retaining structures is, liquid tightness. Liquid-tightness as the name suggest is a measure of resistance a liquid retaining structure have to leakage, this depends largely on crack widths.
In designing containment structures, ensuring liquid tightness is crucial. The structural engineer should discuss and agree upon the liquid tightness requirements with the client. Instead of using colloquial terms like ‘waterproof’ construction, the engineer should specify the acceptable degree of leakage based on the tightness classes outlined in Table 1. This approach will determine the limiting crack widths to be used in the structural design.
Tightness Class | Requirment for Leakage |
0 | Some degree of leakage acceptable or leakage of liquids irrelevant |
1 | Leakage to be limited to small amount. Some surface staining or damp patches acceptable |
2 | Leakage to be minimal. Appearance not to be impaired by staining |
3 | No leakage permitted |
Tightness class 1, the most common for utilitarian water-retaining structures, usually requires only limiting crack widths. However, for tightness classes 2 and 3, limiting crack widths alone is insufficient; additional measures like liners or prestressing will be necessary to meet the requirements.
Achieving liquid tightness also relies on using an appropriate concrete mix and ensuring good workmanship on site. Proper compaction of concrete is essential.
Durability and Selection of Materials
Because liquid retaining in structures remain perpetually in contact with liquid, some which might even be chemical in nature, the material with they’re constructed must comply with certain specification. In designing for durability, concrete should adhere to BS EN 206 and BS 8500 Parts 1 and 2 standards.
Ensuring durability in liquid retaining structures requires well-compacted concrete. Members should generally be at least 250mm thick to allow for good compaction, though thickness should not be excessive, as this increases the required reinforcement. Table 2 outlines the likely exposure classes for different elements.
Element | Likely Exposure Class |
Wall in contact with liquid | Cyclic wet and dry – XC3 and XC4 |
Underside of roofs to reservoirs | Moderately humid environment – XC3 and XC4 |
Surfaces in contact with soil (walls and slabs) | DC class depending on the aggressiveness of the soil |
Unprotected surfaces of walls and roofs | Will depend on the circumstances – XC, XD, XS and XF may all be relevant |
Cover requirements from BS EN 1992-1-1 and BS 8500 typically apply. It is advisable to use a nominal cover (Cnom) of 45mm from the face in contact with liquid and 75mm from any face cast against soil.
Concrete Mix
In designing the concrete mix for liquid-retaining structures, prioritize durability and minimizing the risk of cracking over strength. Achieve watertightness and durability with high-quality concrete, without needing special additives or admixtures. A satisfactory specification for most cases includes:
- Consistence class: S3
- Maximum water-cement ratio: 0.50
- Minimum cement content: 300 kg/m³ (with 20mm aggregate) or 320 kg/m³ (with 14mm aggregate)
- Maximum cement content: 400 kg/m³ for CEM I (OPC) concrete, and 450 kg/m³ with ground granulated blast-furnace slag (GGBS) or fly ash
- Concrete strength class: C30/37
Use cement replacements like GGBS or fly ash to reduce the heat of hydration, aiding in crack control. Suitable types include CEM IIB-V (21–35% fly ash) or CEM IIIA (36–65% GGBS). High proportions of cement replacements can affect early strength and abrasion resistance, potentially impacting the construction schedule.
For structures in contact with aggressive soil, use a mix that resists sulphate attack, such as CEM IIIB or CEM IVB. When storing chemically aggressive liquids, seek expert guidance on the appropriate concrete mix, typically requiring protective liners.
Basis of Structural Design for Liquid Retaining Structures
The design basis of designing liquid retaining structures is taken from BS EN 1990: Basis of structural design. It lays out the design situations and actions a liquid retaining structure must resist.
Design Situations
BS EN 1990 provides general guidelines for design situations. For tanks constructed partially or fully below ground, consider the following:
- Evaluate adverse effects of soil and groundwater pressures on the walls and base during construction and service, typically requiring analysis when the tank is empty.
- When the tank is full, do not account for beneficial effects of soil and groundwater pressures.
Actions on Liquid Containment Structures
Permanent Actions:
- Account for the self-weight of the tank and its contents.
- Include the weight of plant and equipment.
Variable Actions:
- Consider loads due to liquid pressures.
- Include wind loads on above-ground structures.
- Account for snow loads on covered structures.
- Consider uplift forces on underground tanks from groundwater.
- Include lateral loads due to earth and water pressures on underground tanks.
Values of Actions
Establish action values using relevant codes. Designers should typically know the maximum possible depth of stored liquid. It is advisable to perform calculations using the full depth of the tank for a conservative yet reliable design.
Partial Factors on Actions
Refer to the UK NA to BS EN 1990 for partial factors for permanent and variable actions. Tables 3 and 4 provide recommended factors for loads and pressures from retained liquids, assuming the maximum liquid level reaches the top of the walls.
Design situation | Verification | Permanent actions | Loads from contained liquid | Earth and groundwater pressures |
Tank empty | Equilibrum | 0.9 | - | 1.5 |
Tank empty | Strength | 1.35 | - | - |
Tank full | Strength | 1.35 | 1.35 | - |
Design situation | Verification | Permanent actions | Loads from contained liquid | Wind |
Tank empty | Equilibrum | 0.9 | - | 1.5 |
Tank full | Strength – walls and base | 1.35 | 1.35 | 1.5 |
Tank full | Strength – supporting structures and foundations | 1.35 | 1.35 | 1.5 |
Structural Analysis
Having obtained the forces acting on the liquid-retaining structure, they must be analysed for the to determine the internal forces. To carry out the analysis, base the design on elastic analysis without redistribution. In rectangular tanks, consider direct tension in the plane of the walls due to lateral load supported by adjacent contiguous walls. In circular tanks, account for hoop stresses leading to in-plane tension.
Structural Design – Ultimate Limit State
In design liquid retaining structures, the rules as presented in BS EN 1992-1-1 applies fully. However, for particularly shear resistance calculations:
- Calculate the shear resistance of sections not reinforced for shear (VRd,c), considering any tension caused by loading. This includes negative σcp in expressions (6.2.a) and (6.2.b), which reduces shear resistance.
- Use a value of cotθ = 1.0 for shear reinforcement calculations, as recommended by the Eurocode.
Structural Design – Serviceability Limit State
As highlighted in the article opener, the structural design of liquid-retaining structures must consider serviceability limit state with respect to cracking and water tightness.
Crack Widths and Watertightness
Table 5 outlines the crack width limits and recommendations for the water tightness classes from Table 1. Agree on the approach to crack control and its performance implications with the client.
Estimation of Crack Widths
Cracking in liquid retaining structures can for two reasons:
- caused by restraint to movement (imposed deformations)
- caused by loading
Examples of imposed deformations include early thermal effects, autogenous shrinkage, and drying shrinkage. Refer to CIRIA publication C660 for detailed information and formulae for estimating crack widths.
Cracking Caused by Restraint
Although cracking in concrete structures is accepted, it should be controlled so cracks occur at intervals with small widths. This requires a minimum amount of reinforcement in the structural element. Before the first crack occurs, both concrete and reinforcement are in tension. At the crack, only the reinforcement carries the tension. Calculate minimum reinforcement to ensure the reinforcement can transfer the tension without yielding. Stronger concrete requires more reinforcement to achieve controlled cracking. Use the tensile strength of concrete at the expected time of first cracking, often around three days. Figure 1 illustrates the relationship between stress increase and concrete strength over time.
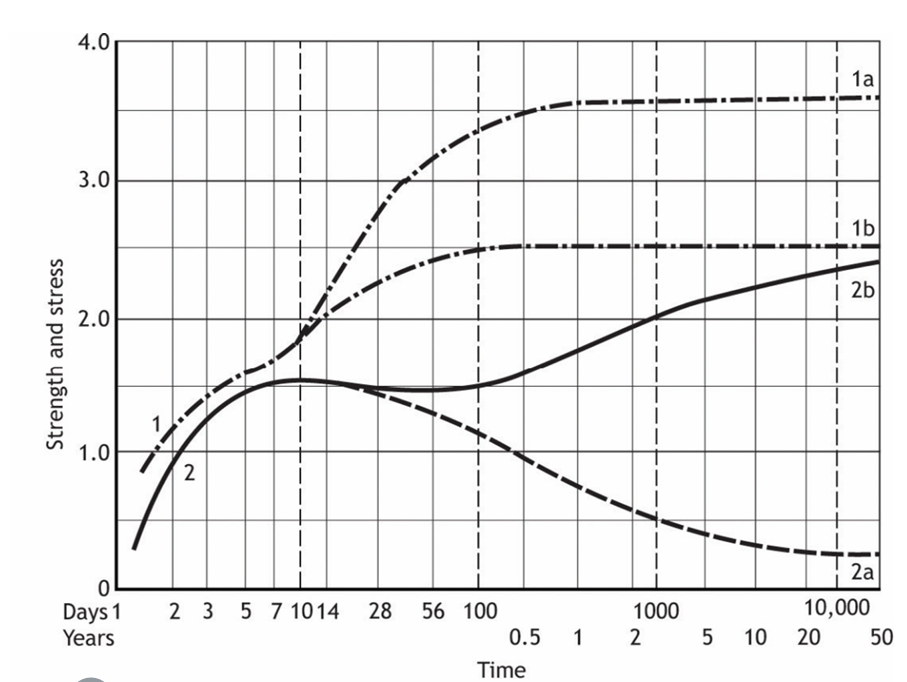
Minimum reinforcement doesn’t guarantee specific crack widths; it’s a necessary but not always sufficient amount for limiting crack widths. Additional reinforcement might be necessary. Restraint to movement is essential for cracking. Restraint can be internal (due to differential expansion, significant in thick sections) or external (end or edge restraint). End restraint causes progressive cracking, with each crack reaching its full width before new cracks form, related to concrete strength and steel ratio. Edge restraint results in cracks distributed by reinforcement and concrete, with crack width depending on restrained strain rather than concrete tensile capacity. Figure 2 shows a typical edge restraint crack pattern.
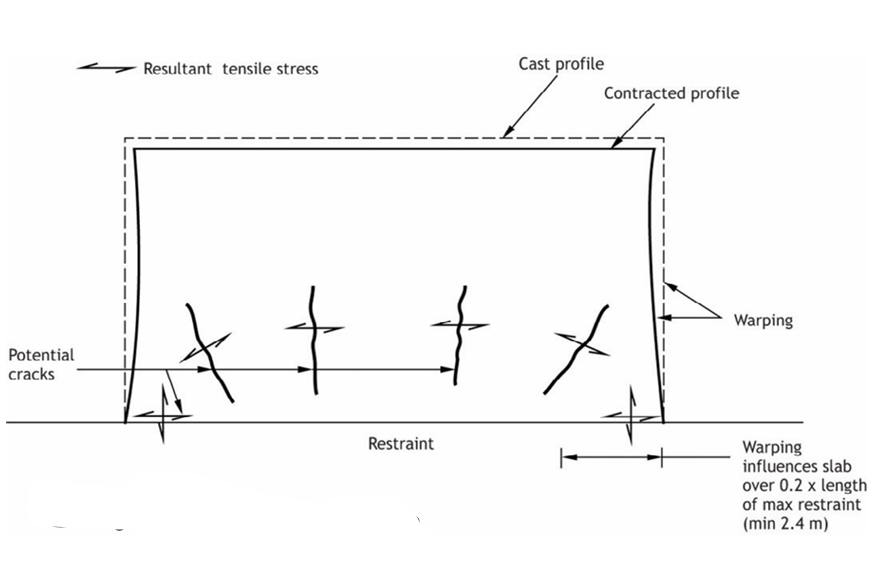
More reinforcement is needed to limit crack width in end restraint members compared to edge restraint members, hence the prohibition of casting in alternate bays.
Cracking Caused by Loading
For cracking caused by loading, use procedures in BS EN 1992-1-1 to control cracking caused by loading.
Minimizing the Risk of Cracking
BS EN 1992-3 suggests strategies to minimize cracking risk. CIRIA publication C660 offers tips for controlling early thermal cracking.
Deflection Control
Deflections are generally not critical. Use procedures in BS EN 1992-1-1, including span-to-depth formulae. Consult manufacturers for strain limitations when applying finishes to the structure.
Construction
Joints
We utilize two types of joints in construction: movement joints to minimize the risk of cracking and construction joints for ease of construction. Provide expansion joints for reversible movements and contraction joints when accommodating only contraction.
To prevent water penetration, minimize the number of joints in water-retaining structures and maintain them for optimal performance. Protect all joints with water bars. If sealing joints is necessary for an added line of defense, have a specialist select the sealants, considering:
- Chemical compatibility with materials or soil in contact
- Expected joint movement
- Ease of repair and replacement
The size of individual pours depends on site constraints, such as access for concreting and the element’s geometry. While the National Structural Concrete Specification provides default pour sizes, these can be modified by agreement between the designer and contractor. Ensure structural continuity at construction joints with no relative movement, passing reinforcement through, and roughening the first pour surface to enhance bond strength and aggregate interlock. Avoid using powerful hammers to prevent dislodging aggregate particles.
Water Bars
Water bars are durable, impermeable strips embedded in concrete during construction, providing a permanent liquid-tight seal across joints. They can be metal strips or proprietary products made of rubber or flexible plastics like PVC (Figure 3).
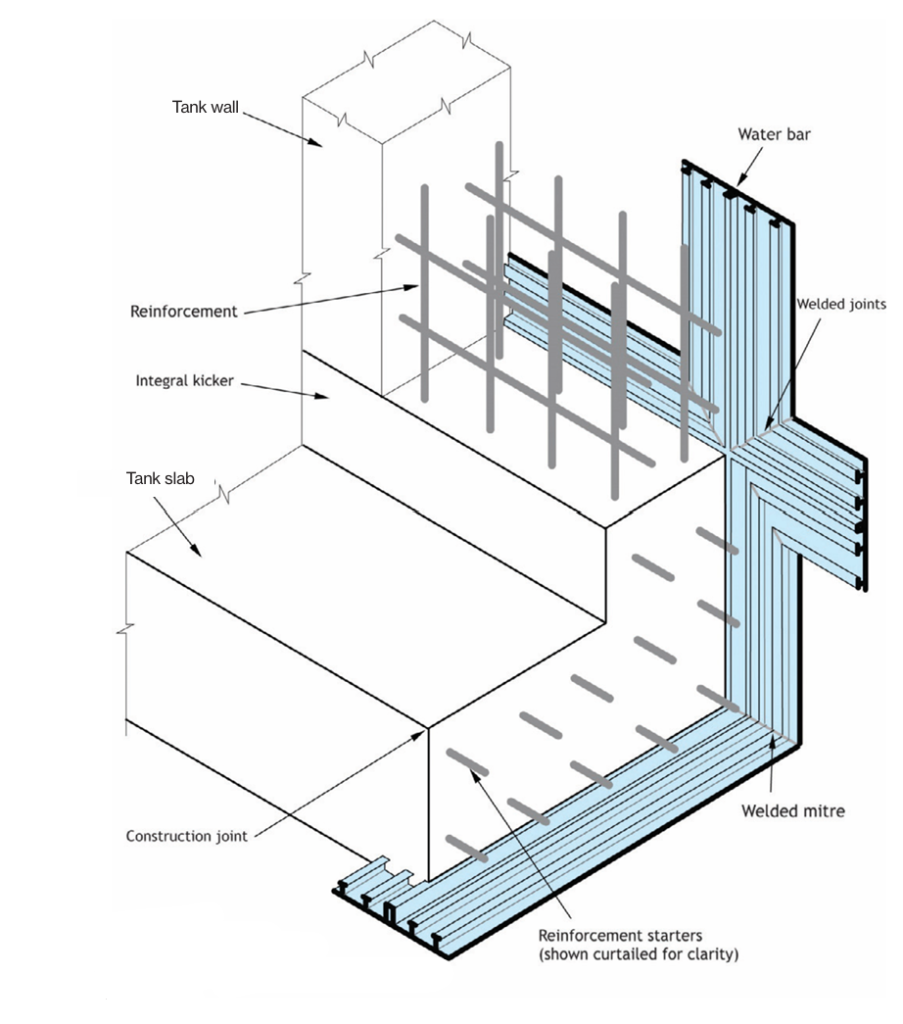
For construction joints (both horizontal and vertical), use a rigid water bar made from a strip of black steel (unpainted and non-galvanized), placed centrally across the joint. In horizontal joints, gently push the water bar in while the concrete is still green. Metal water bars don’t need welding at butt joints; leave a gap equal to aggregate size plus 5mm and place a cover strip overlapping the two water bars with the same gap.
Apply similar detailing at corners. Metal water bars’ stiffness prevents collapsing during concreting, and PVC rear guard water bars are ideal for protecting joints in base slabs cast on the ground.
Also See: A Guide to the Design of Posttensioned Slabs
Sources & Citations
- CIRIA (2007) Publication 660: Early-age thermal crack control in concrete [Online] Available at: www.ciria.org/CMDownload (Accessed: June 2024).
- CIRIA (2007) Publication 660: Early-age thermal crack control in concrete [Online] Available at: www.ciria.org/CMDownload. (Accessed: December 2014)
- Institution of Structural Engineers (2014) Concrete Design Guide: ‘Guidance on design of liquid retaining structures.’ The Structural Engineer. 96(1)