This article will provide a comprehensive look at calculating anchorage and lap lengths according to EC2, breaking down each aspect from basic principles to the final calculation.
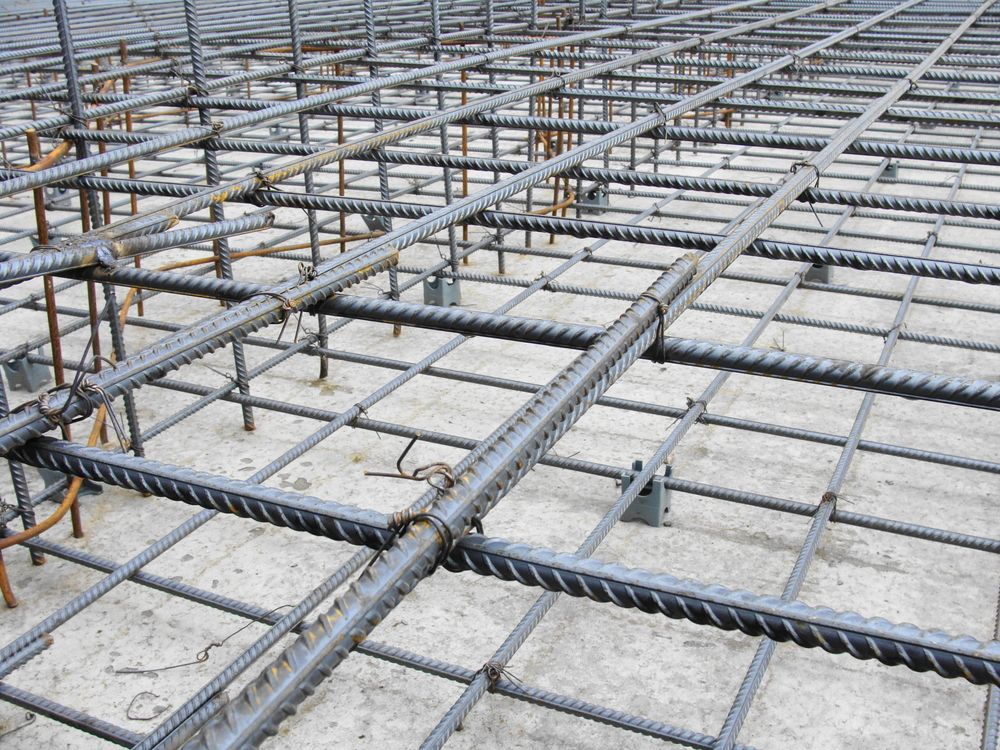
Anchorage and lap lengths are vital for ensuring that reinforced concrete structures perform safely under loading. These elements of reinforcement detailing provide essential guidelines that structural engineers follow to achieve stable, resilient designs. Eurocode 2 (EC2) is one of the primary standards that defines how to calculate these lengths, establishing rules that ensure effective force transfer within reinforced concrete structures.
The concept of anchorage length pertains to the distance required for a steel bar to bond sufficiently with concrete, allowing it to transfer stress safely. Similarly, lap length refers to the required overlap between two bars, ensuring continuity of force transfer within the concrete matrix. Factors such as bar type, concrete strength, bond conditions, and bar stress affect both parameters, making them essential calculations in any reinforced concrete project. Inadequate attention to anchorage and lap lengths could compromise the structure’s stability, potentially leading to structural failures.
This article will provide a comprehensive look at calculating anchorage and lap lengths according to EC2, breaking down each aspect from foundational principles to the final calculation. The article will culminate with a detailed, practical example to illustrate these calculations in a real-world context.
Key Concepts and Definitions
Anchorage Length
Anchorage length refers to the minimum length of a reinforcement bar embedded within the concrete required to develop the bar’s yield strength. This distance allows the bar to bond with the concrete adequately, transferring its load into the concrete and providing the necessary strength to withstand stresses. If the anchorage length is too short, the bar might slip out of place, undermining the structure’s stability.
Lap Length
In cases where a single reinforcement bar cannot span the necessary length of a member, two bars are overlapped to maintain the load-bearing capacity of the structure. This overlapping distance is known as the lap length. Proper lap lengths ensure that the stresses from one bar transfer to the other effectively. The lap length calculation varies depending on whether the bars are in tension or compression, with tension bars requiring longer laps for effective load transfer.
Factors Influencing Anchorage and Lap Lengths in EC2
Bond Conditions (Good or Poor)
The quality of the bond between concrete and reinforcement plays a significant role in determining anchorage and lap lengths. Bond conditions are classified as “good” or “poor,” with good conditions requiring shorter anchorage and lap lengths. Horizontal bars near the top of a thick slab or beam may fall under poor conditions, while vertical or bottom bars generally meet good bond criteria.
Concrete Strength
The characteristic cylinder strength (fck) of concrete impacts bond stress, directly influencing the anchorage and lap length requirements. EC2 provides characteristic tensile strength values based on concrete class (e.g., C25/30, C30/37) to ensure that calculations align with actual concrete performance.
Bar Shape and Confinement
Bar shape (straight, bent, or hooked) and confinement (external reinforcement around the bar) impact the anchorage and lap lengths. EC2 accounts for these variations by providing adjustment factors (α) for each parameter. Straight bars with minimal confinement will need longer anchorage or lap lengths compared to bent bars within well-confined sections.
Coefficients for Anchorage and Lap Length Adjustments
EC2 incorporates coefficients (α1 to α5) to account for varying bond conditions, bar shapes, concrete cover, and transverse reinforcement. These coefficients modify the base lengths for anchorage and lap calculations, adapting them to the specific reinforcement environment. For simplicity, default values can sometimes be used, but using detailed coefficients allows for more efficient, material-saving designs.
Calculation Steps for Anchorage Length to EC2
Anchorage length can be calculated through a series of steps in Eurocode 2, involving the base anchorage formula, modification coefficients, and bond stress. The basic required anchorage length formula is as follows:
l_{b,rqd}=\frac{\phi}{4}\times\frac{\sigma_{sd}}{f_{bd}}
where:
- lb,rqd is the basic required anchorage length,
- ϕ is the diameter of the bar,
- σsd is the design stress,
- fbd is the ultimate bond stress, calculated based on concrete tensile strength and bond conditions.
The final design anchorage length lbd is then determined by applying the coefficients:
l_{bd}=\alpha_1\alpha_2\alpha_3\alpha_4\alpha_5 l_{b,rqd}
Here, each coefficient (α) adjusts for different influencing factors like bar shape, concrete cover, and confinement by transverse reinforcement, following Eurocode’s guidelines.
Calculation Steps for Lap Length to EC2
The lap length calculation shares similarities with anchorage length, adjusting for the overlap between two bars. The formula for lap length is:
l_{0}=\alpha_1\alpha_2\alpha_3\alpha_5\alpha_6 l_{b,rqd}
The coefficient α6 is specifically used for lap length calculations, adjusting based on the number of bars overlapped in a particular section. This coefficient ensures that each bar within the lap area has enough support to transfer the stress effectively.
Worked Example
A construction project involves designing a reinforced concrete beam with tension reinforcement bars. The specifications are as follows:
- Concrete class: C25/30 (characteristic strength fck = 25 MPa)
- Reinforcement bar: Ribbed steel, 20 mm diameter (φ)
- Design stress σsd : 435 MPa
- Bond condition: Good (bars are positioned in an ideal bond location)
- Concrete cover: 30 mm nominal cover
Calculate Ultimate Bond Stress
First, find the design tensile strength fctd, which is a function of concrete strength. For concrete C25/30, EC2 defines fctd as:
f_{ctd}=0.3\times f_{ck}^{2/3} =0.3\times 25^{2/3}=2.6Mpa
Using EC2’s formula for bond stress in good conditions:
f_{bd}=2.25\times η_1\times η_2\times f_{ctd}
2.25\times1\times1\times2.6=5.85Mpa
Calculate Basic Required Anchorage Length (lb,rqd)
Apply the values to the basic anchorage formula:
l_{b,rqd}=\frac{\phi}{4}\times\frac{\sigma_{sd}}{f_{bd}}=\frac{20\times435}{4\times5.85}=372mm
Final Design Anchorage Length (lbd)
Use EC2’s coefficients, assuming straightforward adjustments: α1=1 for a straight bar; α2==1 (nominal cover meets standard); α3=1; α4=1; α5=1.
Thus, this gives:
l_{bd}=1\times1\times1\times1\times1\times372=372mm
Calculate Lap Length (l0)
For the same bar under lap length conditions, assuming a 50% lapping percentage, apply an additional coefficient α6=1.4
l_{bd}=1\times1\times1\times1\times1.4\times372=520mm
Also See: Detailing a Concrete Slabs to Eurocode 2
Conclusion
Anchorage and lap length calculations in reinforced concrete design ensure that bars achieve optimal bonding within concrete structures. Eurocode 2 offers detailed guidance on these calculations, allowing structural engineers to enhance the safety and stability of concrete elements.
- British Standards Institution. (2004). BS EN 1992-1-1:2004 Design of Concrete Structures. London, UK: BSI.
- The Institution of Structural Engineers. (2006). Manual for the Design of Concrete Building Structures to Eurocode 2. London, UK: The Institution of Structural Engineers.