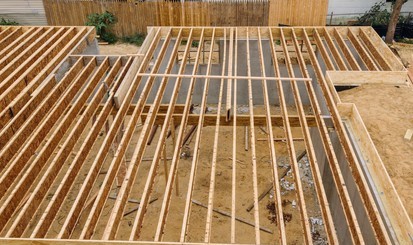
Introduction
Timber joists are one of the most basic structural elements found in many timber frame construction. They are closely spaced timber beams (typically in the range of (450-900mm) used to support a suspended ceiling, timber flooring or sheathings. In this article, we shall discuss the design procedure of timber joist. All advice given will be based on the guidance and recommendations of BS EN 1993-1-1:2004 Eurocode 5 Design of Timber Structures- Part 1-1: General common rules of buildings.
Timber as a structural member is very variable in nature both in strength and stiffness. This was well appraised in a previous article (See: Timber as a Structural Member). The strength of any timber material depends critically on many factors vis a vis, the specie, the rate of growth, the type and number of defect present and the angle of the timber grains. This is fundamental to the design of any timber element, hence for any design in timber, to make effective structural use of the timber materials, they must be classified and assigned into a strength class.
Timber Classification by Strength
The classification of timber by strength depends on whether, after consideration of the critically acclaimed factors in the preceding section, the timber is classified as either a hardwood or softwood. Timber joists are made out of softwoods since they are relatively less dense, easier to work with and readily available. Timber joists are generally available in two classes: C16 & C24. Grade C16 are usually more common, but they are typically weaker, hence readily available and cheaper to procure. C24 on the other hand is relatively stronger, but expensive. They aren’t the favourite except where there is design constraint. For example, where there is a long span and the geometry and depth of flooring needs to be restricted.
For the material properties of the grades of timber as discussed above (See Table 1).
Properties | C16 | C24 |
Characteristic Bending Strength (N/mm2) | 16 | 24 |
Characteristic Shear Strength (N/mm2) | 3.2 | 4.0 |
Parallel Mean Modulus of Elasticity (N/mm2) | 8000 | 11000 |
Mean Density (kg/m3) | 370 | 420 |
Characteristic Density (kg/m3) | 310 | 350 |
Modification Factors of Timber
Timber is a hygroscopic material; it absorbs and release moisture to its surrounding environment depending on the humidity of the environment. Thus, the strength and stiffnesses of any timber material is a direct consequence of the moisture in the environment. To account for this, modification factors are applied to the strength properties of timber by classification. Three service class are defined and the likely environmental conditions are listed as well.
- Service class 1 – intermediate floors, warm roofs, internal and party timber frame walls
- Service class 2 – ground floors, cold roofs, timber frame walls that are against the outer skin of cladding and all other instances where the timber is protected from direct exposure to water
- Service class 3 – external, fully exposed
Load Duration
The first modification factor relates to the duration of the applied load on the timber member. The longer the load duration, the stronger the timber member that must be provided to resist the applied load. Hence a modification factor defined as kmod is usually applied to the characteristic properties of any timber material. The U.K National Annex to BS EN 1995-1-1 classifies the load duration as follows:
- Permanent – more than 10 years, e.g., self-weight including finishes
- Long term – 6 months to 10 years e.g., storage loading
- Medium term – 1 week to 6 months e.g., imposed floor loads
- Short term – less than 1 week e.g., now loads, maintenance access and accidental loads
- Instantaneous – fractions of a second e.g., wind, impact and explosive loads.
Service Class | Permanent | Long Term | Medium term | Short term | Instantaneous |
1&2 | 0.6 | 0.7 | 0.8 | 0.9 | 1.10 |
3 | 0.5 | 0.55 | 0.65 | 0.7 | 0.9 |
The values applied depending on the load duration are produced as (Table 2). When dealing with load combinations, it’s important to check for all conditions and determine the most critical. It’s the load case with the shortest time period that determine the value of kmod. For timber floor joists within a building the typical critical condition is the imposed floor load with the self-weight of the joists and super-imposed dead load. This load condition results in a value of kmod = 0.8 as it is subject to an imposed load, which is defined as medium term, as well as self-weight.
Load Sharing
The next modification factor is ksys which is specifically related to timber joists. Recall timber joist are usually closely spaced with the decking or sheeting distributing the loads between the joist. To account for any uneven distribution and enhance the member resistances, this modification factor is applied to the strength characteristic of the timber member. The value is usually taken to be 1.1 given the flooring is made up of staggered connections and is continuous over two supports. In all other instances the value is taken equal to 1.0.
Enhancement of Shallow Members
Giving the fact that many timber joists will be composed of shallow members and the grading procedure for timber materials, it follows that some form of strength enhancement is obtained for members less than 150mm depth.
In other to gain this, the modification factor kh is applied to the strength characteristics of the timber joist. This is defined as:
{ k }_{ h }={ \left( \frac { 150 }{ h } \right) }^{ 0.2 }\ge 1.3
For all members with section depth greater than 150mm, kh =1.0
Lateral Torsional Buckling
The risk of failure from lateral torsional buckling is mostly not a critical issue in timber joist. This is because in most instances there is restraints to the compression flange of joists from the flooring/sheeting. However, in some instances there are inadequate restraints or no restraints at all, hence the modification factor kcrit is applied to the strength characteristics of the joist. Kindly refer to section BS EN 1995-1-1 for the procedure of deriving kcrit.
Deformation
The last but not the least of the modification is kdef which relates directly with the serviceability limit state of deflection. Since the properties of a timber member depend on the moisture content, it follows also that the deflection of the timber member will be dependent on the service class as discussed above. To take this into account this modification factor is applied to the elastic modulus utilized in the verification of deflection. See Table 3 for typical values of kdef.
Service Class | 1 | 2 | 3 |
kdef | 0.6 | 0.8 | 2.00 |
Member Verification
For most timber joist with sufficient lateral restraint to the compression flange, the design is required to only satisfy flexure and shear at the ultimate limit state, with a verification for deflection and vibration at the serviceability limit state.
Design for Flexure
To design the timber joist against flexure, the applied bending stress must be less or equal to the bending resistance stress. This can be expressed mathematically as:
{ \sigma }_{ m,y,d }\le { f }_{ m,y,d }
Where:
- σm,y,d is the applied bending stress
- fm,y,d is the design bending resistance
{ \sigma }_{ m,y,d }\quad =\frac { { M }_{ y,d } }{ { W }_{ y } } \
{ f }_{ m,y,d }=\frac { { k }_{ h }{ k }_{ sys }{ k }_{ mod }{ k }_{ crit } }{ { \gamma }_{ M } } { f }_{ m,k }
Where:
- My,d is the design bending moment
- Wy is the elastic modulus of the joist, defined as:
- fm,k is the characteristic bending strength (N/mm2)
- γM is the material partial factor of safety taken as 1.3 in the case of solid timber
{ W }_{ y }=\frac { { bh }^{ 2 } }{ 6 }
Design for Shear
Design against shear is ensured by comparing the maximum shear stress against the shear strength of the timber cross-section. To design against shear the following equation must be satisfied.
{ \tau }_{ d }\le { f }_{ v,d }
Where:
- τd is the maximum shear stress
- fv,d is the cross-section shear strength
{ \tau }_{ d }=\frac { 1.5{ V }_{ Ed } }{ bh } \quad ;\quad { f }_{ v,d }=\frac { { k }_{ sys }{ k }_{ mod } }{ { \gamma }_{ M } } { f }_{ v,k }
Where:
- Vd is the design shear force
- h is the depth of the section at point of support
- b is the width of the cross-section
- fm,v is the characteristic shear strength (N/mm2)
- γM is as defined earlier.
The value of fv,d is then multiplied against the effective depth and width of the timber floor joist at the point of support. This is compared against the applied design shear the timber joist has to support. In order to take into account cracking within the timber, the width of the joist is reduced via factor kcr which for solid timber members is taken as 0.67.
Deflection Verification
The final step in the design of a joist is to verify the trial section against deflection. Table 4 gives limiting values based on the variable-imposed loads and permanent actions applied.
Use | Deflection Limit |
Brittle Finishes e.g., floors | Span/250 |
No Brittle Finishes e.g., roofs | Span/150 |
Accidental e.g., fire | Span/20 |
Creep is a significant factor in the deflection of timber structural elements. To allow for this, the instantaneous deflection due to permanent actions is usually increased slightly (1+kdef) while the instantaneous deflection due to imposed variable actions is increased by (1+ψ2,1kdef) assuming only one variable action is acting. The sum of these deflection provides the overall deflection of the joist due to bending.
Worked Example
A timber floor in a new office development is required to span 4.5m, supporting a characteristics-imposed action of 2.5kN/m2. Supposing the joist are to be spaced at 450mm and the self-weight of the timber boards fixed to the top have a self-weight of 0.20kN/m2, verify the adequacy of a 225 x 75 C24 joist to support this floor. Assume the timber boards are able to provide full lateral restraints as well as allowing load sharing between the floor joist and the finish to the floor is brittle.
Worked-Example-on-Design-of-Timber-JoistsCitation
- The Institution of Structural Engineers/TRADA (2010) – Manual for the design of timber buildings structures to Eurocode 5 London: The Institution of Structural Engineers/TRADA
- Porteous, J and Kerman, A. (2007) Structural Timber Design to Eurocode 5 Chi Chester: John Wiley & Sons
- The Institution of Structural Engineer (2012) – Technical Guidance Note Level 2 (18).
Thank You!