This article explores the risk landscape of Modern Methods of Construction (MMC) using a structured approach aligned with the RIBA Plan of Work.
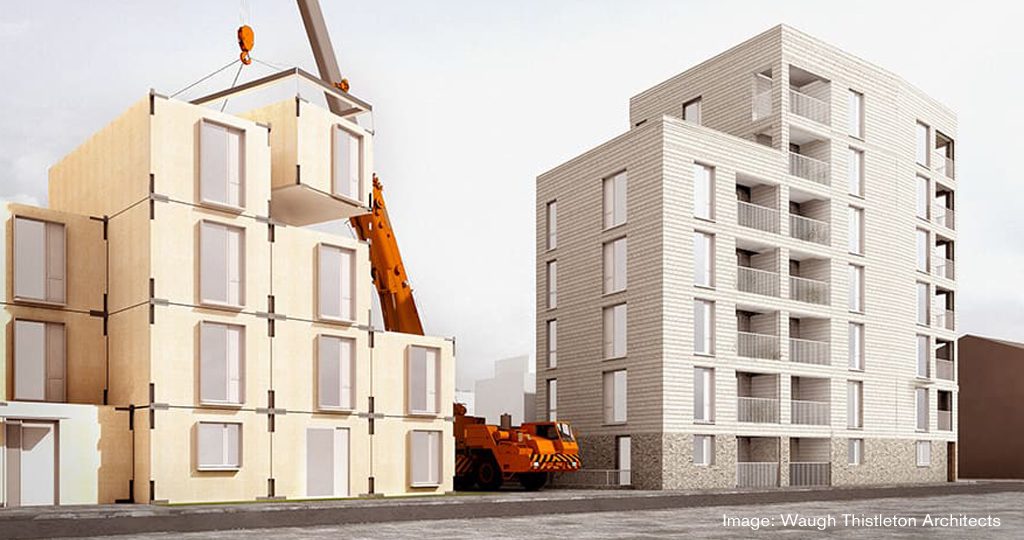
Modern Methods of Construction (MMC) have gained popularity across the built environment sector due to their promise of efficiency. By shifting significant portions of construction off-site, MMC aims to cut costs, reduce on-site risks, and speed up delivery. However, these advantages come with a new category of risks that differ from those in traditional construction.
The success of MMC lies not only in choosing the right system but also in recognising its unique vulnerabilities. These include early design freeze requirements, limitations on post-fabrication changes, specialised insurance challenges, and unfamiliar inspection needs. Neglecting these risk factors could lead to delays, cost overruns, and compromised building performance.
This article explores the risk landscape of MMC using a structured approach aligned with the RIBA Plan of Work. Each stage of a project presents specific opportunities and pitfalls. A clear understanding of these risks empowers teams to reduce uncertainty and improve outcomes from concept to completion.
Understanding Modern Methods of Construction
MMC refers to a spectrum of non-traditional construction practices aimed at improving efficiency, quality, and predictability. It includes off-site techniques like volumetric modular units, panelised systems, sub-assemblies, and pre-engineered components. It also covers on-site innovations such as robotics and lean construction principles.
The UK government’s categorisation framework for MMC separates these into seven defined categories. These range from fully volumetric solutions to site-based process improvements. The fundamental idea is to reduce variability by standardising elements and shifting critical activities into controlled environments.
However, this shift from site-based, linear construction to off-site, parallel processes demands a new way of thinking. Traditional approaches to design development, procurement, inspection, and insurance often prove inadequate. Managing the risks of MMC requires lifecycle thinking and collaboration across the entire supply chain.
Stage 1–3: Early Planning and Conceptual Design
Suitability Assessment at Inception
Before selecting an MMC strategy, the project team must assess whether the site, brief, and stakeholders are compatible. Poor alignment between the MMC system and project needs can lead to design changes, supplier difficulties, and logistical constraints. Not all sites or briefs are suitable for volumetric solutions, for instance, due to access restrictions or spatial complexity.
Carrying out this assessment at RIBA Stage 1 or earlier helps avoid waste and programme disruption. It allows the design to align with system constraints rather than retrofit a modular solution to an unsuitable layout.
Overcoming Perception and Confidence Barriers
Some clients, planners, and insurers view MMC with caution. Concerns about durability, fire safety, and long-term maintenance persist. These can affect funding, approvals, and resale value. Overcoming such doubts requires open communication about quality controls, factory testing protocols, and third-party certifications.
Early engagement with stakeholders builds trust. Design teams should present evidence of accreditation, compliance testing, and previous performance records to reinforce confidence.
Structuring Contracts Around MMC Realities
Traditional contracts assume a fluid design process with late-stage flexibility. MMC demands the opposite. Design decisions need to be finalised earlier to allow for factory production. The contract must define clear freeze points, change management procedures, and product responsibility.
Well-drafted contracts outline what information must be complete before fabrication. They also state who bears the risk of errors after the design is frozen. Without these terms, disputes over late changes or defective products can disrupt delivery.
Stage 4: Technical Design and Specification
Detailing the Design with Precision
Design for MMC requires a higher level of detail earlier in the process. Standardised units rely on consistent, repeatable configurations. Design gaps that might be resolved later in traditional builds must be settled before production begins. Joint detailing, fire stopping, tolerances, and service routing must be fully defined.
Designers must consider load transfer, differential movement, vibration, and robustness. Prefabricated units lack the natural redundancy of traditional builds. The design must provide alternative load paths, ensure diaphragm continuity, and eliminate weak points at interfaces.
Standard Limitations and Compliance Issues
Most jurisdiction still lack comprehensive, unified MMC codes. Although draft standards and guidance exist, they remain under validation. In their absence, many teams turn to international codes or manufacturer specifications. However, such references can fail to address specific regulations or local authority requirements.
This uncertainty increases compliance risk, particularly around fire performance and structural integrity. Designers must consult regulators early, perform rigorous internal reviews, and consider specialist peer input where required.
Coordination Across Disciplines
Coordination between architects, structural engineers, MEP designers, and product suppliers becomes critical. Any clash in assumptions can affect factory work. The interface between modules and traditional elements must be planned in detail. Tolerance overlaps, waterproofing barriers, and fixings all require clear responsibilities and inspection protocols.
Miscommunication can lead to misaligned services, inaccessible maintenance zones, or structural weaknesses. Early, integrated modelling—often using BIM—helps resolve such clashes before fabrication.
Stage 5: Construction and Delivery Logistics
Factory-Based Production Risk
Producing units in a controlled environment improves consistency and safety. However, it also creates the risk of repeat defects. If one production error is not detected early, it can propagate across dozens of units. This risk increases in factories that lack robust quality assurance systems or employ inexperienced labour.
Teams should conduct factory audits before contracting. They must also specify inspection regimes, sample reviews, and test protocols to catch defects early.
Transportation and Handling Hazards
Transporting large volumetric units or fragile panels poses unique risks. Road vibrations, weather exposure, and improper securing can damage units before they reach the site. Some defects may only become visible during installation, when it’s too late to rework.
Planning transport routes, lift schedules, and storage methods helps avoid delays and damage. Designers must provide lifting points, centre-of-gravity diagrams, and resilience to dynamic forces.
On-Site Assembly and Weather Exposure
MMC shortens on-site duration, but installation remains a high-risk phase. On-site assembly requires cranes, accurate positioning, and minimal adjustment flexibility. Even small deviations in plumb, level, or bearing can jeopardise alignment. Weather events during installation can saturate modules before envelopes are sealed.
Contractors must prepare contingency plans. On-site supervision, waterproofing covers, and temporary bracing reduce exposure. Installation sequences must match weather forecasts and site conditions.
Stage 6: Handover and Operation
Documentation and Traceability
MMC projects must provide detailed as-built records. Modules often conceal services, insulation, or fire barriers within sealed units. Future repairs, refurbishments, or fire responses depend on clear records.
Building owners need comprehensive operation and maintenance manuals. These should include layout drawings, materials specifications, fire strategies, and service pathways.
Without these documents, defects can go undetected, and maintenance becomes reactive. Traceability ensures long-term safety and performance.
Maintenance, Retrofit, and Part Replacement
Custom modules or proprietary products may become obsolete. If a component fails, sourcing a match can prove difficult. In some cases, replacing a defective unit may require removing adjacent modules. This can drive high lifecycle costs and limit flexibility.
Designers should avoid overly bespoke assemblies. Where possible, systems should follow open standards, allow safe disassembly, and permit local repairs. Choosing durable finishes and standardised parts extends service life.
Stage 7: Deconstruction and Sustainability Planning
Circular Economy Integration
Modern Method of Construction aligns well with circular economy goals. Units are easier to disassemble, reuse, and recycle—if designed correctly. Yet many systems are not built with deconstruction in mind. Bolted joints may be welded. Finishes may obstruct disassembly. Hidden damage may go unrecorded.
Designers should select materials with known recycling pathways. They must also plan for access, deconstruction sequences, and modular reusability from the outset. The true sustainability of Modern Method of Construction depends on this forethought.
Regulatory and Insurance Considerations at End of Life
At the building’s end of life, insurers and regulators require evidence that demolition or reuse won’t compromise public safety. Fire, asbestos, and structural stability must be evaluated. If fire-resisting barriers are integrated within modules, dismantling without breaching compartments becomes complex.
Teams should retain lifecycle documentation long after handover. This enables safe, responsible reuse or disposal while minimising environmental harm.
Safety and Workforce Considerations
On-Site and Off-Site Safety Risks
Modern Method of Construction shifts physical risks from site to factory, but hazards remain. Heavy lifting, mechanical assembly, and limited workspace can cause injuries. Pinch points, dropped loads, and trip hazards are common in production lines. Forklift misuse, especially during module movement, adds further risk.
Safety training must match each task’s environment. Workers should understand both general risks and system-specific hazards. PPE, safe lifting protocols, and supervision must reflect factory realities.
Fire and Water Risks in Partially Completed Builds
Modules without full enclosure remain vulnerable to arson, water ingress, and theft. Weather can damage unfinished seals. Fires in partially installed units can spread rapidly due to continuous voids or flammable finishes.
Teams must sequence installation to minimise exposure. They should seal penetrations, inspect for pooling water, and secure perimeters at all times.
Conclusion
Modern Methods of Construction offer major benefits in speed, safety, and quality. However, their success depends on recognising and managing unfamiliar risks. Each stage of the project lifecycle introduces unique challenges—from early design freeze requirements to transportation constraints and end-of-life uncertainty.
A structured, collaborative approach unlocks the full potential of Modern Method of Construction. It also protects against the liabilities that can otherwise derail innovative construction. The industry must evolve its tools, expectations, and knowledge to ensure Modern Method of Construction delivers value without compromise.
Also See: Steel and Off-site Construction
Sources & Citations
- Institution of Structural Engineers. (2022). Modern methods of construction: Risk. Retrieved from https://www.istructe.org/resources/guidance/modern-methods-of-construction-risks
- Ministry of Housing, Communities & Local Government (MHCLG). (2019). Modern Methods of Construction: A Definition Framework. Retrieved from https://www.gov.uk/government/publications/modern-methods-of-construction-definition-framework
- Buildoffsite Property Assurance Scheme (BOPAS). (2021). Overview of BOPAS Accreditation. Retrieved from https://www.bopas.org
- Royal Institute of British Architects (RIBA). (2021). RIBA Plan of Work 2020 Overview. Retrieved from https://www.architecture.com/knowledge-and-resources/resources-landing-page/riba-plan-of-work