This article provides an in-depth examination of steel and off-site construction. It discusses how these approaches intersect to improve quality, lower costs, and increase productivity.
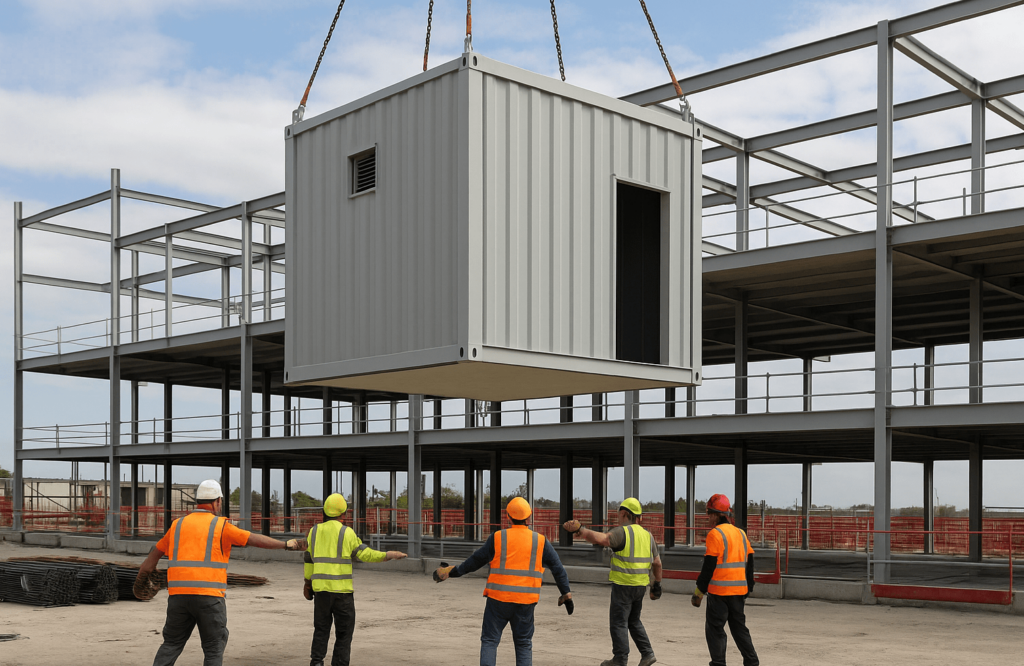
The construction industry continues to face growing pressure to deliver projects faster, safer, and with reduced environmental impact. Traditional on-site methods, while still widespread, often result in delays, waste, and quality variations. Off-site construction—especially when using steel—offers a controlled, efficient alternative that addresses many of these limitations.
Off-site construction moves key building operations from the unpredictable site environment to purpose-built factories. In these factories, teams fabricate components, modules, or even entire rooms in advance. This process allows overlapping of production and site preparation, significantly reducing the time required on-site. By integrating steel, which is strong, recyclable, and consistently manufactured, engineers create durable systems that meet modern building needs.
This article provides an in-depth examination of steel and off-site construction. It discusses how these approaches intersect to improve quality, lower costs, and increase productivity. Each section explores into core concepts, including design stages, fabrication, logistics, tolerance, sustainability, and digital workflows.
Understanding Off-Site Construction in Steel
Off-site construction refers to the process of manufacturing structural elements away from the final building site. In steel construction, this includes components like floor cassettes, columns, and roof trusses. It also includes large volumetric modules that are assembled in factories and delivered complete. These can include integrated MEP services, cladding, and finishes.
Engineers classify off-site approaches by the degree of prefabrication. Low-level prefabrication includes repetitive steel members or factory-welded frames. Mid-level approaches use open panels with pre-installed services. The highest level involves closed volumetric modules ready for immediate use. These approaches reduce on-site operations and enhance safety by limiting manual handling.
Steel is ideal for off-site construction because of its uniformity and strength. Unlike timber, steel has predictable mechanical properties and allows high-precision fabrication. The material supports digital integration, automation, and rapid on-site assembly. It also enables structural spans that would be challenging for concrete or timber without significant weight.
Why Steel Is Ideal for Off-Site Construction
Steel’s mechanical performance, reliability, and adaptability make it the material of choice for off-site projects. Factories can cut, weld, and assemble steel with great accuracy, ensuring components match design drawings exactly. Standardised profiles—such as UB, UC, and RHS—provide flexibility in layout and ease of integration with other systems.
Steel offers a high strength-to-weight ratio. This allows thinner walls, shallower beams, and lighter foundations. These properties reduce transport loads and support taller, wider modules. Steel’s fire resistance can be enhanced through coatings or board systems, making it suitable for regulated spaces such as hospitals and high-rise buildings.
Durability also sets steel apart. Repeated handling during factory assembly, transportation, and crane lifting does not compromise steel components. Minor dents or surface damage can be repaired without structural impact. Galvanising or coating further protects steel from moisture during transport or installation in exposed locations.
Levels of Preassembly and Project Typologies
Engineers must choose the right level of preassembly based on project requirements. For instance, repetitive structures like hotels benefit from full volumetric modular construction. This method allows each room to be built identically in a factory and stacked like building blocks on-site.
In contrast, offices or retail buildings often use preassembled floor cassettes and beam grids. These components reduce on-site welding and speed up superstructure installation. Each project type demands a different balance between off-site work and site assembly.
Higher preassembly requires earlier design freeze. It limits on-site flexibility but improves safety and consistency. Lower preassembly retains design flexibility but requires more site labour. Engineers must balance these priorities to deliver cost-effective, safe, and efficient outcomes.
Importance of Early Engagement in Design
Off-site steel construction success depends heavily on early engineering input. Decisions made during concept design determine the feasibility of modularisation. If engineers join late, designs may require extensive rework or abandon off-site options entirely.
Early input allows engineers to coordinate module layout, lifting strategies, and connection zones. They can assess crane reach, road access, and load paths to ensure safe logistics. In addition, they help architects understand realistic spans, floor zones, and steel depths required for off-site execution.
The factory process demands exact dimensions and tolerances. Last-minute design changes disrupt production and delay delivery. Early collaboration across the design team ensures that layout, detailing, and performance align from the beginning. This leads to smoother workflows and lower cost overruns.
Tolerances and Interfaces: Getting the Fit Right
Off-site systems must connect precisely on-site. Factory tolerances can be within millimetres. Site conditions, however, are rarely as accurate. Settlement, uneven slabs, and weather can all shift dimensions slightly. Engineers must account for this mismatch.
Designers use tolerance allowances in joints to compensate. Slotted bolt holes, elongated connections, and packers help absorb discrepancies. These details ensure that steel frames align correctly during erection. Skipping these details may cause costly site delays and require cutting or welding.
Interfaces with other systems pose further challenges. Steel frames interact with precast concrete, cladding, and MEP services. Interface zones must have enough tolerance to prevent clashes. Engineers should simulate installation using digital models and agree on clear coordination zones for every trade.
Digital Tools in Steel Off-Site Design
Digital design tools enable engineers to visualise, coordinate, and refine steel systems before fabrication. Building Information Modelling (BIM) allows all disciplines to share and review 3D models in real time. Conflicts between systems are resolved early, improving accuracy and coordination.
Digital models also guide automated fabrication. CNC machines read directly from model data to drill, cut, or weld. This reduces interpretation errors and speeds up production. Engineers who provide clean, logical models enable faster and more reliable fabrication.
More advanced systems use parametric design. These tools adjust designs in response to layout changes, geometry, or loading. When an architect shifts a wall, the steel frame updates automatically. This reduces manual redrafting and improves agility during design development.
Transport and Lifting Considerations
Steel modules must withstand transit forces and remain stable during lifting. Engineers must consider maximum road width, height, and axle loads. Modules that exceed limits require escort vehicles or special approvals. This adds cost and complexity to delivery.
Modules also experience stresses during loading, acceleration, and braking. Engineers must check their resistance to torsion, racking, and vibration. Temporary bracing or support frames may be required to keep geometry intact during movement.
On-site lifting presents similar challenges. Cranes must lift modules without inducing excessive deflection or twisting. Lifting lugs, slings, or frames must be designed and tested. Engineers often simulate lifting paths and load conditions to validate the method. They must also coordinate crane access, swing radius, and obstruction clearance.
Procurement and Programme Benefits
Steel off-site systems offer significant programme gains. Foundations, drainage, and services can begin while modules are fabricated. This parallel working shortens the total project duration and frees up skilled trades for other work.
Procurement also becomes more predictable. Repetition enables bulk orders, locking in prices and delivery slots. Fabricators can optimise workflow, reduce downtime, and use lean methods. This results in lower waste and consistent quality.
However, these benefits depend on timely decision-making. Fabricators require early commitment. Long lead times on steel, coatings, or specialist fixings demand good planning. Delays in drawing approvals or changes in layout can cause expensive disruption. Therefore, early design freeze is essential.
Common Pitfalls and How to Avoid Them
Off-site projects sometimes fail to meet expectations due to poor coordination. A common error is underestimating site tolerance issues. Engineers may design for perfect geometry without allowing real-world variance. During erection, frames do not align, and costly rework follows.
Another issue arises when design teams isolate disciplines. Structural engineers may work independently of services or architectural teams. This results in clashes between beams and ducts or modules and stair cores. Engineers must lead integration and use shared digital tools.
Late design changes also undermine off-site efficiency. If a layout changes after modules are in fabrication, teams may need to scrap components. Change control must be strict. All stakeholders must agree to key decisions before production begins.
Sustainability and Life-cycle Considerations
Off-site construction using steel supports multiple sustainability goals. Factory production generates less waste, and most waste is recycled. Off-cuts return to the supply chain instead of landfill. Scrap steel becomes new products, reducing raw material demand.
Fewer site deliveries reduce traffic emissions. Modules arrive once, already finished. This cuts journeys for trades, deliveries, and waste collection. Sites stay cleaner and quieter, reducing disruption in urban areas.
Steel frames also support circular economy goals. At the end of use, modules can be disassembled, moved, or reconfigured. Steel components can be melted down or reused with minimal processing. Engineers must design for disassembly by using bolts, reusable fixings, and logical assembly sequences.
Conclusion
Steel and off-site construction deliver faster, cleaner, and more controlled projects. Engineers must engage early to support layout planning, tolerance design, and coordination. They must work closely with fabricators and understand factory limitations. Off-site steel systems are not a shortcut. They demand planning, rigour, and collaboration. But when used correctly, they transform construction from a reactive process into a proactive delivery system.
Also See: Fire Safety in Steel Framed Buildings: Engineering Approaches and Applications
Sources & Citations
- Institution of Structural Engineers. (2020). Steel and Off-Site Construction. The Structural Engineer, Vol. 98, Issue 6.
- CIRIA. (2019). Delivering Offsite Construction: Strategy, Governance and Capacity. Report C727.
- Lawson, R.M., Ogden, R.G., & Bergin, R. (2008). Application of Modular Construction in High-Rise Buildings. Journal of Architectural Engineering.
- WRAP. (2007). Offsite Construction Case Studies. Waste and Resources Action Programme.
- MPA. (2021). Modern Methods of Construction and Steel. Steel Construction Institute.