This article explains how to prepare robust specifications and minimize associated risks. It details why old specifications cannot simply be reused, outlines best practices, and explores the legal and practical benefits of well-prepared documents
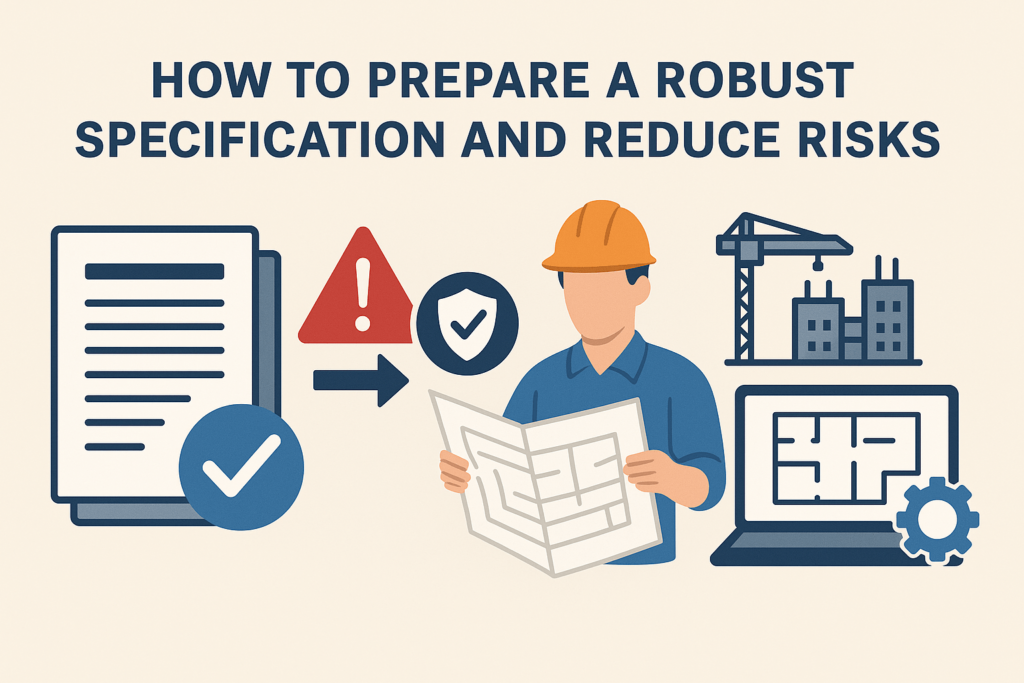
Construction specifications play a critical role in any building project. They form a blueprint for the materials, methods, and standards to be followed. A clear and detailed specification communicates the vision and requirements of the design. It binds architects, engineers, contractors, and stakeholders in agreement. They serve as a binding agreement among stakeholders, ensuring all parties remain aligned on project goals and quality.
In “A Background to Construction Specifications” we learned that a good specification defines quality expectations for materials and workmanship. It also establishes inspection and testing plans linked to those standards, enhancing quality control during execution. These advantages underscore why specifications are invaluable. A strong spec provides clarity and reduces ambiguity across project documentation. It also mitigates project risks, enabling precise cost estimates and reducing delays and disputes.
A robust specification serves as a proactive risk management tool. Well-written specifications can prevent project delays, cost overruns, and disputes. They force the project team to address potential problems early. For example, one study found 15% of projects suffered delays due to poor specifications. By preparing a thorough specification, teams can greatly reduce those risks. This article will explore how to build a resilient specification that boosts project quality and minimizes risk.
Understanding Construction Specifications
By formal definition, a specification is a document that lays out detailed requirements for products, materials, and systems. According to ISO 6707‑2:2017, a specification “gives out detailed requirements for a product, material, process, or system”. It acts as a rulebook for the project. In practice, specifications complement the drawings. They capture information that drawings alone cannot express. A well‑written specification has broad benefits. One expert emphasizes that “everyone in the contract game benefits from a well‑written specification”. A good specification spells out details clearly and cuts guesswork. Moreover, the specification is part of the contract and sets the stage for execution.
Construction specifications can take several forms. Some are descriptive, listing exact products and installation methods. Others are performance‑based, stating only functional outcomes. For example, a performance specification might require HVAC to maintain a certain temperature. It would allow contractor flexibility in how to achieve it. Prescriptive specifications go further by specifying precise material mixes or component details. Projects often blend these approaches to balance clarity with innovation. In all cases, the goal is to document the design intent and quality requirements fully before construction begins.
Key Components of a Robust Specification
A complete specification covers the full scope of work and quality requirements. It should begin with a clear statement of project scope and objectives. This defines the goals and expectations for the construction project. Next, it details the materials and methods to be used. For example, the spec will list the materials, finishes, and installation procedures for each element. This ensures consistency and quality control in how the work is performed.
The specification must also define quality standards and performance criteria. It should specify acceptable tolerances, required testing, and inspection protocols. For example, it may set out how to test concrete strength or the cleaning requirements for metal surfaces. By linking inspection plans to the specification, the team can verify that materials and workmanship meet the documented standards. This reduces the chance of substandard work, warranty claims, or litigation. Finally, a specification should include contractual and legal considerations. It defines responsibilities, liabilities, and dispute‑resolution mechanisms. Clear assignment of these elements in the spec helps avoid misunderstandings and conflicts later on.
Writing Clear and Effective Specifications
The language of a specification must be precise and active. Each requirement should use a clear subject and verb (for example, “the contractor shall install…”), rather than passive voice. Avoid vague terms and synonyms. Specifiers often capitalize defined terms (such as “Hot Dip Galvanizing” or “Approved Installer”) and use them consistently. This approach prevents misinterpretation. Provisions should use mandatory words (such as “shall” or “must”) to state requirements. Each clause should stand alone. If one reads it in isolation, it must still convey a complete requirement. Write short sentences with one idea per clause to avoid ambiguity.
Organize the specification logically. Use a recognized classification or numbering system (for example, Uniclass or CSI MasterFormat) to group sections. Start each section with a brief descriptive header. Number clauses sequentially to maintain consistency. For example, section numbers can match drawing detail keys or BIM element codes. Include a table of contents and consistent headings so anyone can find information easily. Avoid mixing topics in one section; subdivide by system or trade (for example, separate sections for concrete, steel, timber, finishes, etc.). Cross‑reference drawings or BIM models whenever possible, so users can connect the specification with the visual information.
Preparing the Specification Document
Start the specification process early in design. Gather all relevant project data: drawings, material data, client requirements, and applicable codes or standards. By involving the specifier from the beginning, the team ensures that project intentions are captured as soon as decisions are made. Coordinate with architects, engineers, and the quantity surveyor. They can provide notes on materials or performance expectations. In complex projects, use a checklist to make sure no key component is overlooked.
Use templates or software as guides. Many firms use standard templates or digital platforms that follow industry best practices. These tools often include built‑in libraries and validation rules to help ensure completeness. Populate each section with the gathered data. For each system or material, include a description, specifications, and execution requirements. Reference industry standards explicitly by number. For example, specify ASTM, BS, or ISO codes for material grades and performance thresholds. Avoid generic statements; instead give exact specifications for what is needed. For instance, if a fastener is required, list its size, material, and any special coatings. If a material can be substituted, the spec should require approval and specify the criteria (such as “or equal approved”). Once drafted, circulate the specification for internal review. Involve senior designers and a constructability reviewer to check for completeness and coherence. Revise the draft based on feedback. This thorough preparation prevents many issues on site.
Managing Risks Through Specifications
A robust specification is a powerful risk management tool on a construction project. As one expert notes, specifications are “the compass that navigates you through possible pitfalls”. They establish expectations upfront and eliminate uncertainty. By documenting detailed requirements, a spec forces the team to think through potential problems before work begins. Every requirement written into the specification preempts a potential risk. For instance, specifying certified fire‑rated materials avoids safety hazards due to untested products.
One of the most common risks is project delay. In fact, data show about 15% of construction projects are delayed due to poor specifications. A detailed spec minimizes this by clearly defining scope and timing. According to a recent survey, 80% of specifiers say that a good specification prevents delays. Similarly, cost risk is reduced. When requirements are clear, bids and budgets become more accurate. Without specifications, cost estimates become unreliable, so a solid spec avoids hidden extras later.
Specifications also mitigate quality and legal risks. Clearly stating quality standards and tests means contractors know what is expected. In practice, absence of such guidance leads to ambiguity and disputes. One commentary bluntly notes, “Without specifications, you risk project quality”. Another analysis points out that lack of specifications leads to ambiguity and misinterpretation. It adds that this ambiguity can cause inconsistencies, disputes, and delays. When quality criteria are defined, the team can identify and fix any failures. Linking test plans to the spec makes verification systematic. This reduces the chance of defects, warranty claims, or litigation.
A specification also enforces safety and compliance. It should reference all relevant codes, standards, and certifications. For example, many regulations require specific product certifications.
Collaboration and Specification Review
A specification is not created in isolation. It should be reviewed by all key stakeholders. Architects, engineers, contractors, and even the owner should have input. Early contractor review can catch constructability issues or missing information before bidding. In best practice, architects invite contractors, owners, product reps, and consultants to review project specs during design. This open dialogue helps catch ambiguities or omissions in advance. Clear communication ensures that requirements are understood and achievable. It also strengthens buy-in. When contractors know exactly what is expected, they make fewer costly assumptions or substitutions. Engaging the team in this way mitigates risk and helps keep the project on track.
Using Digital Tools and Standards
Advances in technology have transformed specification writing. Building Information Modeling (BIM) can link specification data directly to the 3D model. With BIM, stakeholders can visualize the project in 3D and see the specified elements in context. BIM can also integrate with other software, enhancing collaboration among the construction team and reducing miscommunication Beyond BIM, specialized specification software (such as NBS Chorus) offers cloud-based libraries and templates. These tools enforce consistency and store all clauses in a central database. A single update then propagates to all related documents, reducing the chance of contradictory information. Using digital platforms also supports the golden thread of information: the data is secure, accessible, and kept up-to-date.
Use recognized classification codes for efficiency. Many firms adopt a uniform system (for example, Uniclass or CSI MasterFormat) so all trades follow the same organization. Linking classification codes across BIM, specifications, and drawings helps software cross-reference items correctly. Finally, leverage digital collaboration. For example, use cloud drives and version control so the design team can annotate the spec. This creates an audit trail of decisions and updates. Such transparency helps satisfy audit requirements and maintain quality control throughout the project.
Specification in Contracts and Construction
The specification is a formal part of the contract documents. It is included in the bidding documents so contractors’ price their work against it. Once bids are received, any questions about the specification should be resolved by addenda. After contract award, the specification becomes binding on all parties. During construction, the specification guides inspections and approvals. If contractors find missing or conflicting information, they submit a request for information (RFI). The design team should respond in writing, typically by updating the specification or issuing an addendum. Maintaining a clear revision process keeps the specification up to date. Make sure each issued spec has a title page with revision number and date. That way, everyone is using the correct, latest version.
Avoiding Common Specification Pitfalls
Even a well-prepared specification can fail if misused. A frequent complaint is that specs are written but then not followed on site. As one article notes, “nobody ever reads” a specification unless it is highlighted. To avoid this, emphasize the spec’s importance in pre-construction meetings and require contractors to acknowledge the key requirements. Do not leave the specification static as design changes. If drawings or decisions change, update the spec. Failure to do so leads to conflicts: contractors might follow an outdated spec while drawings show something else. Always issue updated specification addenda when changes occur.
Another pitfall is unclear wording. Terms like “suitable” or “as directed” are vague unless defined. Use plain language and specify numbers and units wherever possible. For example, give numerical values for tolerances and dimensions. Avoid contractions or lists of multiple requirements in a single sentence. On the other hand, over‑specification can be counterproductive. Micro-managing every detail can stifle contractor flexibility and innovation. Instead, state required outcomes clearly and allow alternatives where acceptable. This balanced approach keeps the specification practical and reduces arguments.
Conclusion
A robust construction specification is a cornerstone of project success. It brings clarity, quality, and accountability to every phase of construction. By fully documenting all requirements, the specification minimizes uncertainty and aligns all parties. It covers everything from scope and materials to testing and legal terms. Investing time in preparation pays off by preventing delays, cost overruns, poor workmanship, and disputes. A strong specification improves coordination and compliance, and it becomes part of the project handover package. It guides future maintenance and changes, ensuring that the building continues to meet its design criteria. Ultimately, the benefits are clear: better communication, smoother execution, and safer, higher-quality buildings. Specifiers who follow these principles will reduce risk and save time and money in the long run. Well-crafted specifications reflect the professionalism of the design team and build trust with owners and contractors. They protect the project’s schedule, budget, quality, and safety.
Also See: A Background to Construction Specifications
Sources & Citations
- Institution of Structural Engineers. (2019). Business Practice Note No. 24: How to Prepare a Robust Specification and Reduce Risks. The Structural Engineer, Vol 97, Issue 5.
- Institution of Structural Engineers. (2019). A Background to Construction Specifications. Structures Centre.
- NBS. (2020). Specification writing best practices. Retrieved from thenbs.com
- CIRIA. (2019). Effective Specification Strategies for Construction Projects. CIRIA Report C780